
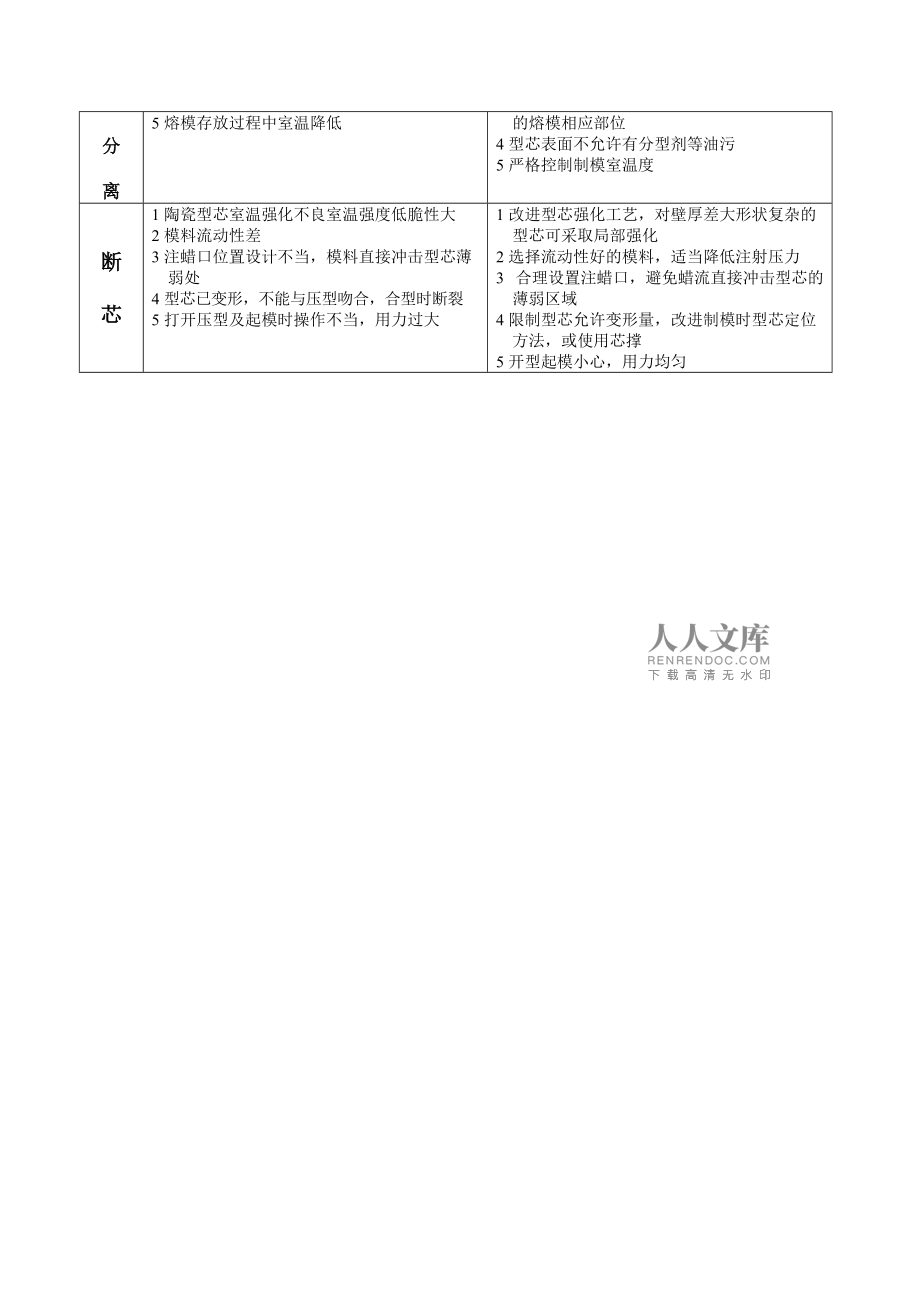



版權(quán)說明:本文檔由用戶提供并上傳,收益歸屬內(nèi)容提供方,若內(nèi)容存在侵權(quán),請進(jìn)行舉報或認(rèn)領(lǐng)
文檔簡介
1、熔模常見缺陷及防止方法(水玻璃工藝)缺陷名稱產(chǎn) 生 原 因防 止 方 法表面粗糙1蠟膏攪拌不充分或溫度不均勻2模料壓注溫度低3分型劑不均勻或過多4壓注壓力不足或中斷5壓型溫度過低1充分?jǐn)嚢柘灨啵娱L保溫回性時間2嚴(yán)格控制模料壓注溫度3分型劑涂抹應(yīng)薄而均勻4提高壓注壓力5適當(dāng)提高壓型溫度缺肉1壓型溫度或模料溫度過低2壓注壓力太小,壓注速度太慢3模料注入口位置不當(dāng)或注入口的截面積太小4模料注入量不夠5壓型排氣不良1提高壓型或模料溫度2提高注射壓力和速度3改進(jìn)注入口位置,或增大注蠟孔截面積4增加模料注入量5增設(shè)排氣通道冷隔1壓型溫度和模料溫度低2分型劑太多或不均勻3注蠟口小或位置不當(dāng)1提高壓型和模料
2、溫度2分型劑涂抹應(yīng)薄而均勻3增大注蠟口或改變模料注入位置流紋1分型劑的用量過多,或涂抹不勻2分型劑選擇不當(dāng)或變質(zhì)3注射壓力小,注射速度太慢4壓型溫度低1分型劑用量應(yīng)適當(dāng)涂抹應(yīng)薄而均勻2合理選擇分型劑并確保分型劑質(zhì)量3提高注射壓力和注射速度4提高壓型溫度縮陷1注蠟時模料或壓型溫度過高2模料的收縮率大3注射壓力小或保壓時間不足,模料得不到充分補償4注蠟口小或位置不當(dāng)5起模早,冷卻不充分6熔模結(jié)構(gòu)設(shè)計不和理,壁厚差懸殊7熔模局部太厚1降低壓型或模料溫度2換用收縮率小的模料3提高注射壓力和延長保壓時間,達(dá)到充分補縮4增大注蠟口或改變位置,以利補縮5延遲起模,熔模要及時充分冷卻6改進(jìn)熔模結(jié)構(gòu)設(shè)計壁厚應(yīng)盡
3、量均勻7在厚大部位預(yù)置冷蠟塊(又稱蠟芯)裂紋1起模時間過長,熔模收縮受阻2模料收縮率大或太脆3壓型設(shè)計不正確,或起模操作不當(dāng)4壓型溫度過低,使熔模冷卻太快5壓注時模料溫度偏高1控制熔模在壓型中的冷卻時間2改用收縮率小韌性好的模料3改進(jìn)壓型設(shè)計,增大圓角或起模斜度,起模時用力要均勻4提高壓型的工作溫度5降低壓注時模料的溫度鼓包1模料中攪入了氣體2起模太早,被壓縮的氣包膨脹3熔模沒有及時冷卻,或冷卻不充分4制模室溫度過高1配置模料時應(yīng)避免裹入過多的氣體2適當(dāng)延長保壓時間3從壓型取出的熔模應(yīng)及時冷卻并控制冷卻時間4嚴(yán)格控制制模室工作溫度變形1起模過早,2壓型設(shè)計不良3熔模存放狀態(tài)不良,引起變形4熔模
4、存放溫度過高5熔模存放時間過長6熔模收縮率偏大1延長保壓時間,或采用校正模2改進(jìn)壓型設(shè)計增加起模裝置注意起模操作3熔模存放狀態(tài)合理或采用存放胎具4控制熔模存放溫度5合理按排生產(chǎn),縮短熔模存放時間6改用收縮率小的模料芯蠟分離1模料收縮率較大2制模時型芯溫度和模料溫度均偏低3型面結(jié)構(gòu)有大面積光滑表面4型芯表面有油污5熔模存放過程中室溫降低1選用收縮率小的模料2壓制熔模前將型芯加熱至3050,或提高模料的壓注溫度3起模后立即用手按壓有大面積光滑型芯表面的熔模相應(yīng)部位4型芯表面不允許有分型劑等油污5嚴(yán)格控制制模室溫度斷芯1陶瓷型芯室溫強化不良室溫強度低脆性大2模料流動性差3注蠟口位置設(shè)計不當(dāng),模料直接
5、沖擊型芯薄弱處4型芯已變形,不能與壓型吻合,合型時斷裂5打開壓型及起模時操作不當(dāng),用力過大1改進(jìn)型芯強化工藝,對壁厚差大形狀復(fù)雜的型芯可采取局部強化2選擇流動性好的模料,適當(dāng)降低注射壓力3 合理設(shè)置注蠟口,避免蠟流直接沖擊型芯的薄弱區(qū)域4限制型芯允許變形量,改進(jìn)制模時型芯定位方法,或使用芯撐5開型起模小心,用力均勻水玻璃型殼的缺陷及防止方法缺陷名稱產(chǎn) 生 原 因防 止 措 施表面蟻孔1涂料中硬脂酸配比過低,蠟?zāi)1砻嫖催M(jìn)行脫脂處理2涂料潤濕性差3涂料的粉液比低,流杯粘度小,涂層薄,面層撒砂粒度粗1模料中硬脂酸配比不能低于50%2模料進(jìn)行脫脂處理3涂料中加入適當(dāng)配比表面潤濕劑4提高涂料粉液比,提高
6、流杯粘度5降低面層撒砂粒度表面圓珠狀小孔1表面層涂料攪拌時卷入過多氣體而產(chǎn)生氣孔2未加消泡劑1用發(fā)泡力低的表面潤濕劑2涂料中加入適量的消泡劑3用毛筆刷涂或用壓縮空氣噴吹氣泡橘子皮和皺疤1熔模表面局部涂料堆積,涂層過厚。且未經(jīng)自然干燥。致使涂料在化學(xué)硬化時,表層因硅凝膠形成急劇收縮,而涂料內(nèi)層未經(jīng)充分硬化,故而在表面形成皺皮2在面層涂料與熔模表面之間常有鹽類和水分濃集,導(dǎo)致硬化不良,脫蠟時型殼內(nèi)表面松散并出現(xiàn)突起和凹坑,形似橘皮狀1表面層涂料粘度不要太高,增加涂料流動性2避免蠟?zāi)1砻婕熬植客苛隙逊e,應(yīng)使涂料分布均勻3表面層浸涂料撒砂后,先經(jīng)一定時間的自然干燥后,再進(jìn)行化學(xué)硬化4表面層的化學(xué)硬化要
7、充分型殼分層和鼓脹1涂料撒砂后,表面有浮砂2表面層撒砂的粒度過細(xì),砂中粉塵過多或砂粒受潮含水分過多3型殼表面層化學(xué)硬化后風(fēng)干時間過短,殘留硬化劑過多4涂料粘度過大涂層過厚,涂層中間未硬化1表面層撒砂要干燥,無粉塵,水分小2表面層撒砂粒度不要太細(xì),并防止浮砂堆積3表面層涂料粘度不宜太大,防止涂料堆積,涂層要充分硬化4表面層硬化后的干燥時間要充分,殘留硬化劑要少5以氯化鋁和氯化鎂硬化的型殼在浸第二層涂料前須進(jìn)行沖水,涼干以增強層間結(jié)合型殼裂紋1浸涂料后未能撒上砂粒的部位易產(chǎn)生裂紋2涂料粘度過低,粉料加入量過少,涂層過薄3涂層未經(jīng)充分硬化4脫蠟水溫度低,脫蠟時間過長5水玻璃模數(shù)過低,密度小6型殼層數(shù)
8、不足1控制水玻璃的模數(shù)密度及涂料芬液比和粘度2控制硬化劑的濃度溫度及硬化時間等工藝參數(shù)3提高脫蠟水溫度至9598,縮短脫蠟時間4適當(dāng)增加型殼層數(shù)5大件型殼在制殼時可用鐵絲加固,以增加高溫強度型殼變形型殼變形大多在脫蠟焙燒或澆注時產(chǎn)生1涂料的粘度過大,涂層過厚,涂料堆積2硬化劑濃度低溫度低硬化時間太短,硬化不足3脫蠟水溫度低,脫蠟時間過長4焙燒時型殼受擠壓或溫度過高1控制涂料粉液比和粘度2避免涂料局部堆積3控制硬化劑濃度,溫度和硬化時間4縮短脫蠟時間,適當(dāng)提高脫蠟水溫度(9598)表面析出物1氯化銨硬化的型殼,脫蠟后干燥時,型殼內(nèi)在硬化反應(yīng)時生成的鹽分及殘留的氯化銨硬化劑,隨水分蒸發(fā)擴散遷移到型
9、殼表面上來,并沿析出孔道堆集生長成茸毛狀物質(zhì),其中4/5是NaCI,約1/5是NH4CI2氯化鋁硬化的型殼(尤其是聚合氯化鋁硬化),硬化反應(yīng)時產(chǎn)生的鋁膠AI(OH)3,通常鋁膠以你散狀態(tài)分布于型殼中,若硬化時間不足,在脫蠟時脫蠟水的PH值高,就可能使殘留的氯化鋁析出難溶的鋁膠附于型殼內(nèi)外表面上,形成析出物1型殼脫蠟后存放時間不要太長,應(yīng)及時焙燒澆注2水玻璃密度不宜過大3涂料粘度不要過高4氯化鋁硬化劑的PH值要適當(dāng),硬化時間要充足5脫蠟水應(yīng)保持酸性熔模鑄件常見缺陷及防止方法名稱缺陷特征產(chǎn) 生 原 因防 止 方 法氣孔鑄件中出現(xiàn)明顯孔穴,孔內(nèi)光滑1型殼焙燒溫度低和保溫時間不足2澆注系統(tǒng)設(shè)計不和理,
10、型腔排氣不暢3金屬液脫氧出氣不充分1提高型殼焙燒溫度和延長保溫時間2增設(shè)排氣孔或采用底注式澆道3熔煉過程充分脫氧皮下氣孔鑄件經(jīng)加工后出現(xiàn)的光滑孔洞1爐料不干凈或使用過多的回爐料2熔煉過程中金屬液氧化吸氣,脫氧不充分3型殼表面與金屬液發(fā)生反應(yīng)1清潔爐料并減少回爐料用量2嚴(yán)格控制熔煉工藝,加強脫氧3選用合適的耐火材料渣氣孔夾雜物與氣孔并存1爐料不干凈或回爐料過多2熔煉過程脫氧不充分3鋼液含氣量多4型殼焙燒不足1清潔爐料并減少回爐料用量2嚴(yán)格控制熔煉工藝,加強脫氧3鎮(zhèn)靜鋼液4充分焙燒型殼縮孔和縮陷鑄件上由于補縮不良造成的孔洞,形狀不規(guī)則,孔壁粗糙1鑄件結(jié)構(gòu)不和理,有難以補縮的熱節(jié)2澆冒口補縮作用欠佳
11、3澆注溫度過高1改進(jìn)鑄件結(jié)構(gòu),減少熱節(jié)2合理設(shè)計澆冒口,使鑄件定向凝固,增大補縮壓頭3降低澆注溫度縮松鑄件冷卻較慢處產(chǎn)生成片細(xì)小分散孔洞1鑄件結(jié)構(gòu)不和理,難以充分補縮2澆冒口設(shè)計不和理,補縮作用欠佳3澆注溫度過低4鑄型的溫度低,鑄件冷卻速度過快1改進(jìn)鑄件結(jié)構(gòu),減少熱節(jié)2合理設(shè)計澆冒口,使鑄件定向凝固,增大補縮壓頭3適當(dāng)提高澆注溫度和鑄型溫度熱裂裂紋沿晶界生長,表面有氧化顏色1鑄型溫度低,冷卻速度過快2型殼退讓性差,阻礙收縮3鑄件結(jié)構(gòu)不和理,壁厚相差懸殊,過渡突變,應(yīng)力過大4澆注補縮系統(tǒng)設(shè)計不合理,造成鑄件局部 過熱或收縮受阻1提高鑄型溫度,減緩鑄件冷卻速度2改善型殼退讓性和潰散性3改進(jìn)鑄件結(jié)構(gòu)
12、減小壁厚差,平緩圓滑過渡4改進(jìn)澆注系統(tǒng)設(shè)計5選擇熱裂傾向小的合金和鋼種冷裂裂紋大多穿過晶粒,表面光亮1鑄件結(jié)構(gòu)不和理2澆注系統(tǒng)設(shè)計不和理3鑄件在搬運和清砂過程中受撞擊4鑄件在矯正時操作不當(dāng)或未退火1改進(jìn)鑄件結(jié)構(gòu)和澆注系統(tǒng)設(shè)計,減小收縮應(yīng)力2避免撞擊和拋甩鑄件3矯正前退火,并改進(jìn)矯正操作4減少型殼層數(shù),并改善退讓性5降低鑄件的冷卻速度,例如單殼可改用填砂澆注金屬刺鑄件表面出現(xiàn)密集或分散的小刺1面層涂料粉液比低或粘度低2涂料與蠟?zāi)1砻鏉櫇裥圆?蠟?zāi)1砻嫦炐嘉聪磧?面層撒砂料太粗1提高面層涂料粉液比和粘度2增加面層涂料潤濕劑加入量3認(rèn)真清洗蠟?zāi):臀g刻4減小面層撒砂料粒度粘砂鑄件表面有粘砂層,經(jīng)噴砂后
13、顯示有凸起的毛刺或凹坑1面層用的耐火粉料和撒砂料雜質(zhì)含量過高2制殼耐火材料或粘結(jié)劑選用不當(dāng)3澆注溫度過高4澆注系統(tǒng)設(shè)計不和理,造成型殼局部過熱1降低涂料中粉料和撒砂料中的雜質(zhì)含量2選用適當(dāng)?shù)哪突鸩牧虾驼辰Y(jié)劑3降低澆注溫度4改進(jìn)澆注系統(tǒng)設(shè)計,減少局部過熱表面麻坑鑄件清理或拋丸后,局部出現(xiàn)密集的點狀凹坑1澆注時金屬液和鑄型的溫度偏高,鑄件冷卻速度慢2鑄件冷卻環(huán)境氣氛氧化性太強3水玻璃型殼中殘留的鈉鹽太多1降低鑄型和金屬液的溫度,加快鑄件冷卻速度2在鑄型的周圍人為的造成還原性氣氛3合理選用耐火材料和粘結(jié)劑4充分焙燒型殼5嚴(yán)格制殼工藝,保證硬化,風(fēng)干充分夾雜物鑄件上存在與基體成分不同的物質(zhì),包括涂料層
14、,砂粒,硅酸鹽,皂化物1型殼面層涂料干燥,硬化不良2涂料層結(jié)合不牢,在制殼和焙燒過程中面層涂料剝落3型殼強度低,承受不了鋼液的沖擊而損壞4型殼脫蠟后放置時間短,水分多或焙燒時升溫快而損壞5操作不慎,由澆口杯掉入砂?;蚱渌s物6模組焊接質(zhì)量不良,涂料滲入接縫處形成飛翅7模料中混入涂料粉,砂粒,皂化物等雜物1面層涂料充分干燥.硬化2降低第二層涂料的粘度3提高型殼強度4延長脫脂后型殼放置時間5脫蠟前仔細(xì)清理澆口杯邊緣;澆注前用吸塵器將型殼中的雜物吸出;采用二次焙燒法,即一次焙燒后,用熱水仔細(xì)清洗型殼內(nèi)腔再進(jìn)行二次焙燒6改進(jìn)操作,消除蠟?zāi):附犹幍目p隙,或采用浸封模料浸封7認(rèn)真過濾和處理回收模料氧化夾雜
15、多見于大氣熔煉和澆注的耐熱合金,不銹鋼鑄件,其形狀呈細(xì)小片狀或網(wǎng)絡(luò)狀1爐料不干凈,在熔煉過程中脫氧不充分2澆注系統(tǒng)擋渣作用差3澆注溫度低,不利于氧化物浮出1清潔爐料,加強脫氧2采用底注式澆道3提高鑄型溫度和澆注溫度4出鋼前用聚渣劑除渣5采用真空熔鑄或過濾凈化渣孔鑄件的內(nèi)部或表面夾有渣料,拋丸后鑄件表面形成孔洞1渣料太稀,出鋼前未扒凈2爐嘴上的雜物未清理干凈3澆注時擋渣不好4澆注系統(tǒng)擋渣作用差1適當(dāng)調(diào)整渣料增大粘度便于扒渣,并使用聚渣劑2認(rèn)真清理爐嘴上的浮砂或雜物3澆注前適當(dāng)鎮(zhèn)靜鋼液以利浮渣4澆注時擋好渣5改進(jìn)澆道設(shè)計或采用過濾器鼓脹在鑄件較大平面上局部凸起1制殼用耐火材料的雜質(zhì)高,粘結(jié)劑的高溫
16、性能差,使型殼在高溫金屬液的作用下產(chǎn)生變形2澆注溫度過高3硅酸乙酯型殼面層硬化不透1使用雜質(zhì)含量低的耐火材料,選用合適的粘結(jié)劑,提高型殼高溫強度。2降低澆注溫度或采用填砂法澆注3延長面層涂料氨干時間,增加氨氣濃度4增設(shè)工藝孔表面凹陷鑄件表面局部凹陷1蠟?zāi)1砻婵s陷2型殼分層,型殼面層向內(nèi)鼓脹1用表面無縮陷的蠟?zāi)?嚴(yán)格制殼工藝,避免涂料堆積,保證硬化,風(fēng)干充分3仔細(xì)清理浮砂 ,降低過渡層涂料粘度鑄瘤鑄件表面凸起的金屬小瘤1涂料中的氣泡未被排除2涂料時蠟?zāi)9战腔驕喜厶幱袣馀輮A在涂料中1涂料鎮(zhèn)靜或真空除氣2涂料時用毛刷或氣嘴仔細(xì)排除夾在蠟?zāi)9战翘幍臍馀菔笪茶T件表面有不規(guī)則的淺溝條紋1型殼面層熱膨脹系數(shù)
17、大而背層小,在加熱過程中面層涂料開裂翹起2涂料面層和背層結(jié)合不牢1合理選用型殼面層和背層的耐火材料2仔細(xì)清理浮砂,降低過渡層涂料的粘度冷豆在鑄件表面嵌有未完全熔合的金屬顆粒1澆注系統(tǒng)設(shè)計不合理,澆注時金屬液產(chǎn)生飛濺2澆注時沖擊力過大,金屬液在型腔內(nèi)產(chǎn)生飛濺1合理設(shè)計澆注系統(tǒng),使金屬液平穩(wěn)進(jìn)入型腔2澆注時,適當(dāng)降低澆包與鑄型間的距離,避免產(chǎn)生飛濺冷隔鑄件上邊緣圓鈍的穿透或不穿透縫隙1澆注溫度或鑄型溫度低2內(nèi)澆道截面積小3澆注速度慢4澆注時斷流1提高澆注溫度和鑄型溫度2合理設(shè)計內(nèi)澆道3提高澆注速度4防止斷流澆不到鑄件殘缺或棱角不清晰1澆注溫度或鑄型溫度低2澆注速度慢3鑄型排氣不暢4內(nèi)澆道設(shè)計不當(dāng),金屬液流程過長1提高鑄型和澆注溫度2提高澆注速度3增設(shè)排氣孔或改善型殼透氣性4改變內(nèi)澆道的位置或增加數(shù)量脫碳鑄件表面層碳的含量低于基體1澆注時金屬液和鑄型的溫度偏高,鑄件的冷卻速度慢2鑄件冷卻環(huán)境氣氛氧化性太強1適當(dāng)降低鑄型和金屬液的溫度,加快鑄件的冷卻速度2在鑄型的周圍,人為
溫馨提示
- 1. 本站所有資源如無特殊說明,都需要本地電腦安裝OFFICE2007和PDF閱讀器。圖紙軟件為CAD,CAXA,PROE,UG,SolidWorks等.壓縮文件請下載最新的WinRAR軟件解壓。
- 2. 本站的文檔不包含任何第三方提供的附件圖紙等,如果需要附件,請聯(lián)系上傳者。文件的所有權(quán)益歸上傳用戶所有。
- 3. 本站RAR壓縮包中若帶圖紙,網(wǎng)頁內(nèi)容里面會有圖紙預(yù)覽,若沒有圖紙預(yù)覽就沒有圖紙。
- 4. 未經(jīng)權(quán)益所有人同意不得將文件中的內(nèi)容挪作商業(yè)或盈利用途。
- 5. 人人文庫網(wǎng)僅提供信息存儲空間,僅對用戶上傳內(nèi)容的表現(xiàn)方式做保護(hù)處理,對用戶上傳分享的文檔內(nèi)容本身不做任何修改或編輯,并不能對任何下載內(nèi)容負(fù)責(zé)。
- 6. 下載文件中如有侵權(quán)或不適當(dāng)內(nèi)容,請與我們聯(lián)系,我們立即糾正。
- 7. 本站不保證下載資源的準(zhǔn)確性、安全性和完整性, 同時也不承擔(dān)用戶因使用這些下載資源對自己和他人造成任何形式的傷害或損失。
最新文檔
- 2025年度行政合同行政主體特權(quán)在緊急情況下的適用合同4篇
- 2025版小學(xué)操場運動設(shè)施更新與維修合同3篇
- 體育會展客戶關(guān)系管理考核試卷
- 光纖通信在智能電網(wǎng)故障診斷中的應(yīng)用考核試卷
- 2025年土地轉(zhuǎn)讓合同
- 2025版停車場消防設(shè)施建設(shè)與維護(hù)服務(wù)合同3篇
- 2025版木工材料研發(fā)與勞務(wù)合作合同范本3篇
- 2025年寫作創(chuàng)作分期付款合同
- 2025年加盟代理合約協(xié)議
- 2025年家庭矛盾仲裁協(xié)議
- 油氣行業(yè)人才需求預(yù)測-洞察分析
- 《數(shù)據(jù)采集技術(shù)》課件-Scrapy 框架的基本操作
- 2025年河北省單招語文模擬測試二(原卷版)
- 高一化學(xué)《活潑的金屬單質(zhì)-鈉》分層練習(xí)含答案解析
- 圖書館前臺接待工作總結(jié)
- 衛(wèi)生院藥品管理制度
- 理論力學(xué)智慧樹知到期末考試答案章節(jié)答案2024年中國石油大學(xué)(華東)
- 2024老年人靜脈血栓栓塞癥防治中國專家共識(完整版)
- 四年級上冊脫式計算100題及答案
- 上海市12校2023-2024學(xué)年高考生物一模試卷含解析
- 儲能電站火災(zāi)應(yīng)急預(yù)案演練
評論
0/150
提交評論