



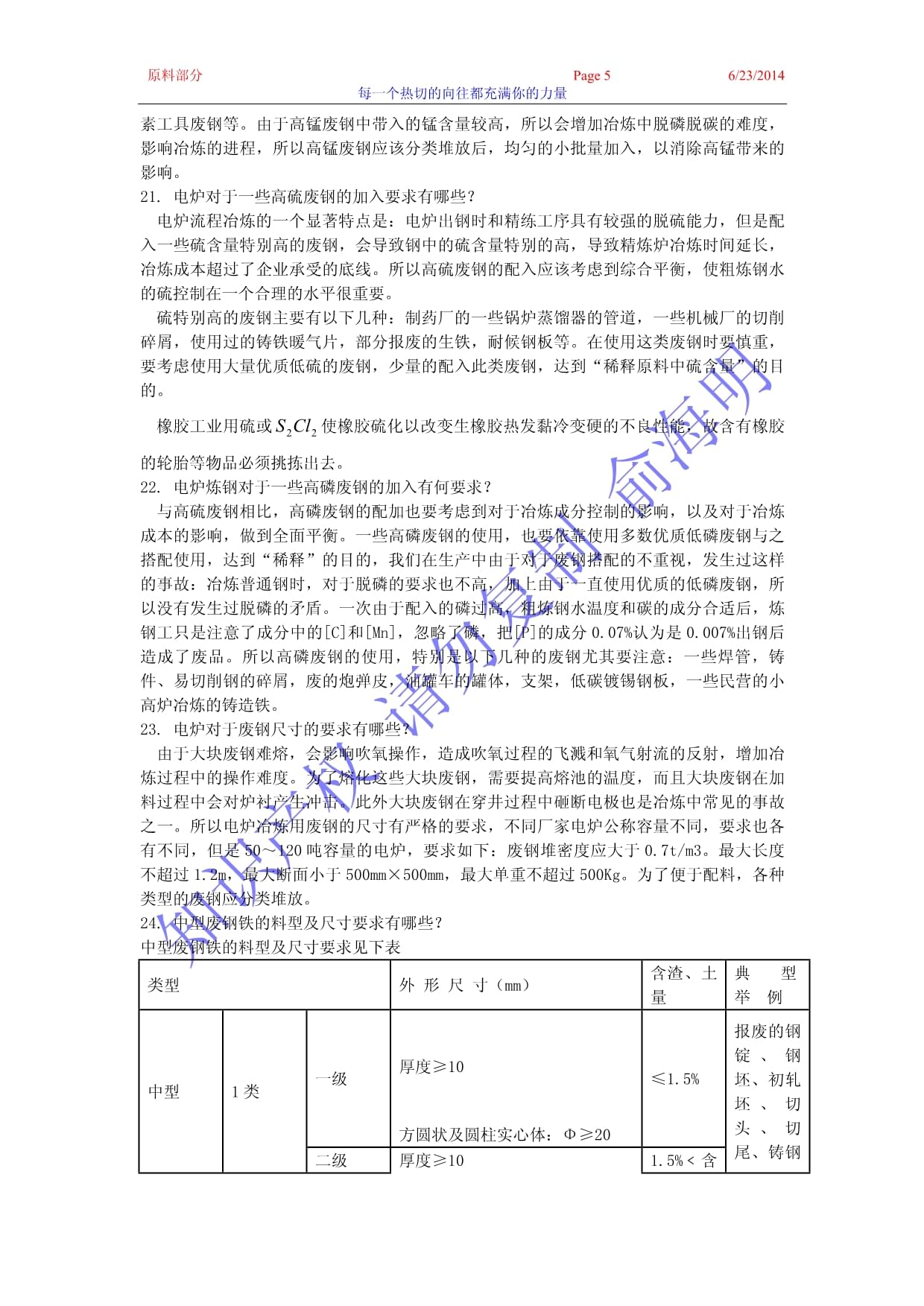
版權(quán)說明:本文檔由用戶提供并上傳,收益歸屬內(nèi)容提供方,若內(nèi)容存在侵權(quán),請進(jìn)行舉報(bào)或認(rèn)領(lǐng)
文檔簡介
原料部分PagePAGE37 DATE\@"M/d/yyyy"6/23/2014每一個(gè)熱切的向往都充滿你的力量第二部分電爐的原料基礎(chǔ)知識(shí)問答電弧爐煉鋼用原材料有哪些?答:電爐煉鋼使用的原料主要有廢鋼鐵料主原料和石灰,白云石等渣輔料,以及造渣使用的發(fā)泡劑,脫氧劑和合金化使用的各類合金。在一些傳統(tǒng)的小電爐還使用氧化劑等原料。其中廢鋼主原料分類較多包括:廢鋼、生鐵、返回廢鋼、直接還原鐵等。造渣材料包括石灰、白云石、螢石等。氧化劑包括氧化鐵皮,鐵礦石等。為什么裝料時(shí)要有一定布料方法,怎樣正確布料。答:裝料操作是電爐冶煉過程重要的一環(huán),它對(duì)爐料的熔化、合金元素的燒損以及爐襯的使用壽命等都有很大影響。冶煉對(duì)廢鋼鐵的一般要求是什么?答:(1)廢鋼的表面應(yīng)清潔少銹。(2)廢鋼中不應(yīng)混有鉛、錫、砷、銅、鋅等有色金屬。(3)化學(xué)成分要明確。(4)廢鋼塊度要合適。電爐的加料順序有何要求?廢鋼的加料順序如下表所示廢鋼類型高度方向的規(guī)則主要原因輕薄料料藍(lán)底部減少廢鋼對(duì)于爐底的沖擊中型廢鋼中部優(yōu)化爐料的熱模型結(jié)構(gòu)生鐵中下部生鐵的熱容較大,難以熔化大塊廢鋼中下部防止折斷或者砸斷電極重型廢鋼中下部防止折斷或者砸斷電極加入廢鋼的準(zhǔn)則輕薄料(生鐵)→中型廢鋼或者重型廢鋼、或者渣鋼→中型廢鋼→輕薄料簡述直流電爐的布料原則,并且說明為什么?廢鋼配料順序的一般性規(guī)則見下表廢鋼配料的冷區(qū)示意圖和熱區(qū)示意圖熱區(qū)包括偏弧區(qū)和吹氧產(chǎn)生的點(diǎn)熱源區(qū)域。分別為1、2、6、3.冷區(qū)包括距離熱源和反應(yīng)熔池較遠(yuǎn)的區(qū)域,包括4、5.廢鋼的類型適合區(qū)域禁止區(qū)域大塊廢鋼熱區(qū)、偏弧區(qū)(2、3、6)1、EBT、5區(qū)域中型廢鋼沒有限制沒有限制輕薄料沒有限制沒有限制生鐵0、2、3、5、6區(qū)域1、EBT、5區(qū)域渣鋼(大包鑄余等)2、3、6區(qū)域0區(qū)域粒鋼禁止在電爐煉鋼過程中加入禁止使用熱壓快0、2、3、6區(qū)域1、4、5直接還原鐵0、2、3、6區(qū)域1、4、5含氧化鐵的返回廢鋼0、2、3、61、4、5冶煉不同的鋼種,配廢鋼的基本要求有哪些?廢鋼配料的基礎(chǔ)要求如下表鋼種要求對(duì)主原料的要求備注普通鋼種無要求低磷不配渣鋼、渣鐵成品[P]max≤0.010%低S、N鋼不允許全廢鋼冶煉,不配渣鋼、渣鐵,鐵水采用低硫鐵水成品[S]max≤0.003%低殘余元素鋼廢鋼中轉(zhuǎn)爐返回廢鋼比>45%成品[Cu]max≤0.15%低S、N、殘余元素鋼不允許全廢鋼冶煉,廢鋼中的返回廢比>45%,不配渣鋼、渣鐵。成品[S]max≤0.010%成品[Cu]max≤0.15%極低殘余元素鋼不允許全廢鋼冶煉,廢鋼全部采用返回廢鋼成品[Cu]max≤0.05%特殊鋼種不允許全廢鋼冶煉,廢鋼全部采用返回廢鋼,不配渣鋼、渣鐵,鐵水采用低硫鐵水成品[Cu]max≤0.05%成品[S]max≤0.003%備用電爐開第一爐的配料如何配加,為什么?電爐開第一爐的爐料,需要考慮到電爐新修砌的耐材不能夠受到較大的沖擊,尤其是爐底和爐墻,此外第一爐的冶煉還要考慮到收得率,留鋼量的關(guān)系,一般比正常的配料多10%到20%,廢鋼以小型重廢鋼為主。廢鋼配料為什么講究料型的搭配?不同料型的廢鋼,收得率不同,雜質(zhì)元素含量也不同,廢鋼的堆比重量也不同。合理的搭配料型,主要是將廢鋼的加入體積控制在合理的經(jīng)濟(jì)范圍以內(nèi),減少加料的次數(shù),減少爐蓋旋開造成的熱損失,降低能耗縮短冶煉周期,此外通過料型的搭配,將配入電爐的爐料中間有害雜質(zhì)元素的含量控制在一個(gè)合理的范圍內(nèi),減少各類的渣料消耗,減輕操作難度,所以料型的搭配,是電爐煉鋼最為關(guān)鍵的一個(gè)環(huán)節(jié)。國外電爐行業(yè)云:煉鋼始于廢鋼,足見料型搭配之關(guān)鍵。為什么說潮濕的爐料對(duì)于電爐冶煉的危害最大?潮濕的廢鋼,不僅增加鋼中的[H]含量,最為主要的是潮濕的廢鋼在加料過程中,會(huì)引起爆炸傷人,或者炸壞設(shè)備,這種情況在有熱兌鐵水的時(shí)候尤為明顯,此外潮濕的廢鋼中間的水蒸發(fā)吸熱,會(huì)造成冶煉電耗增加,故潮濕之廢鋼對(duì)于電爐煉鋼危害最甚。為什么含有耐火材料的大塊廢鋼不能夠在電爐煉鋼中使用?幾乎所有的普通耐火材料導(dǎo)電性都很差,這些廢鋼加入電爐以后,成為不導(dǎo)電物質(zhì)(NCC),造成不導(dǎo)電折斷電極,同時(shí)冶煉開始不起弧,需要人工處理。增加了工人的勞動(dòng)強(qiáng)度,也影響了冶煉周期。同時(shí)含有較多耐材的廢鋼熔化速度受耐材的影響,難以正常的熔化,會(huì)發(fā)生堵塞出鋼口等事故,所以含有明顯不導(dǎo)電耐火材料的廢鋼應(yīng)該處理后入爐是很必要的。夾雜有耐火材料的典型廢鋼有哪些?這類廢鋼主要指:渣鐵,連鑄的中包鑄余,模鑄的中鑄管,湯道,地溝鐵,事故鋼包的冷鋼,鋼包澆完的包底,鋼包,鐵水包的包口鐵等。電爐煉鋼使用潮濕廢鋼有何危害?如何預(yù)防?由于潮濕的廢鋼在加料時(shí)可能引起爆炸,不僅會(huì)對(duì)爐襯的壽命產(chǎn)生影響,而且會(huì)損壞水冷盤或者設(shè)備,引起生產(chǎn)中斷。在質(zhì)量上,還會(huì)引起鋼中氫含量的增加。由于缺少廢鋼的烘烤和干燥處理的手段,新疆八一鋼鐵股份公司電爐廠,在每年在春季和下雪的季節(jié),都會(huì)頻繁的發(fā)生因?yàn)閺U鋼潮濕或者夾雜冰雪引起的爆炸事故,輕的事故會(huì)引起加料的中斷,重大的引起爆炸后,廢鋼四處飛濺,最遠(yuǎn)的達(dá)到離爐體60米遠(yuǎn)的地方,水冷盤被炸漏水。主控室的玻璃被經(jīng)常損壞。所以電爐廠電爐冶煉用廢鋼應(yīng)保持干燥,其中不得夾帶冰雪。最基本的要求是廢鋼中在潮濕不可避免時(shí),不能有滴水現(xiàn)象的出現(xiàn)。廢鋼加工后在儲(chǔ)運(yùn)過程中要防止廢鋼的受潮。電爐煉鋼對(duì)于密閉容器和爆炸物的要求有哪些?由于密閉容器、爆炸物在受熱后也會(huì)引起爆炸,所以要杜絕密閉容器、爆炸物得入爐。這一點(diǎn)在使用可疑廢鋼或者軍火銷毀時(shí),要更加小心,在使用前要予以清除或者處理,比如液化氣罐,氣體壓力容器。使用前要切割開罐體或者瓶體后方可使用,銹蝕的炮彈狀,地雷狀的廢鋼要做特殊處理后才能夠使用。我們曾經(jīng)發(fā)生過110t1號(hào)行車在加入了第一批廢鋼料后,由于混入了銹蝕嚴(yán)重,外形變形的反坦克壓發(fā)地雷,加完廢鋼后,2號(hào)110t行車緊接著進(jìn)行兌如鐵水的操作,在兌加鐵水進(jìn)行到三分之一后,發(fā)生了爆炸,爆炸后廢鋼拋入高空20米高的行車磨電道后引起短路,導(dǎo)致生產(chǎn)中斷達(dá)5小時(shí)左右的事故。電爐煉鋼對(duì)于含有油脂類廢鋼的加入量有哪些要求?由于油脂類在高溫下會(huì)裂解成氫和碳,所以含油的廢鋼會(huì)導(dǎo)致鋼液的氫含量增加,還會(huì)產(chǎn)生大火,燒壞設(shè)備。新疆八一鋼鐵股份公司直流電爐廠發(fā)生過5起以上的因?yàn)閺U鋼中易燃物過多,引起行車加料后易燃物產(chǎn)生的火焰過大引發(fā)大火,行車來不及開走,火焰沖上鋼絲繩,直到行車本體,引起大火的事故。直接后果是行車損壞,鋼絲繩的壽命下降等惡性事故,所以含油脂類較多的廢鋼在冶煉高質(zhì)量鋼或者對(duì)于氫有敏感性的鋼中要杜絕此類廢鋼的加入,此類廢鋼主要指車床加工后的切屑,汽車的油箱,帶潤滑的軸類廢鋼,橡膠輪胎等。電爐對(duì)于含有有色金屬的廢鋼有何要求?答:對(duì)于有色金屬的要求由于一些有色金屬元素Cu、Ni、As、Cr、Pb,Bi,Sn,Sb在鋼中大多數(shù)都是有害的元素(除非是特殊鋼種有要求),而且不容易去除,這些有害元素的存在,主要是惡化鋼材和鋼坯的表面質(zhì)量,增加熱脆傾向,使低合金鋼發(fā)生回火脆性,降低連鑄坯的熱塑性,在含氫的氣氛里發(fā)生應(yīng)力腐蝕,降低耐候鋼和耐熱鋼的壽命和熱塑性,降低IF鋼的深沖性能。其中痕量元素(錫Sn、銻Sb、砷As、鉛Pb和鉍Bi,統(tǒng)稱五害元素)對(duì)鋼的影響機(jī)制主要表現(xiàn)集中為:
(1)在鋼坯的表面形成低熔點(diǎn)液相,形成網(wǎng)狀裂紋(紅脆);
(2)在晶界(或亞晶界)偏聚削弱了鐵的原子間力,脆化了晶界(回火脆)。(3)砷As在一些核工業(yè)用鋼部件上使用后會(huì)產(chǎn)生強(qiáng)烈的同位素轉(zhuǎn)變引起的輻射。(4)有些有色金屬,比如Pb等,在爐底會(huì)發(fā)生沉降積累現(xiàn)象,除了影響鋼材的質(zhì)量外,對(duì)于爐底的壽命,特別是直流電爐的爐底壽命影響特別突出,據(jù)有關(guān)文獻(xiàn)報(bào)道由于有色中金屬的沉積導(dǎo)致的穿爐事故已經(jīng)成為生產(chǎn)中的主要矛盾之一。所以含有有色金屬的廢鋼,必須做處理后方可以加入電爐冶煉,主要的手段之一就是每次加入量控制在一個(gè)特定的值,使入爐有色金屬的含量控制在鋼中成分要求的安全范圍以內(nèi)。新疆八一鋼鐵股份公司第三煉鋼廠就發(fā)生過銅含量超標(biāo)制成銅廢的事故,以及鉻,鎳,銅三者之和超標(biāo)廢的事故。國內(nèi)一些廠家對(duì)于鋼材有色金屬的含量要求見下表目前已有一些去除鋼中有色金屬元素的有效方法,對(duì)于特鋼企業(yè)來講是一個(gè)明智的選擇,這些手段有:(1)添加抑制元素,添加抑制元素硼鈦,它們一會(huì)增加銅在奧氏體中的溶解度或者是與銅在晶界處形成合金,來減少或者消除銅含量超標(biāo)所造成的熱脆性,添加稀土元素(比如添加鑭和鍶)可以有效抑制鋅等帶來的偏聚現(xiàn)象。表:國內(nèi)一些廠家對(duì)于有色金屬的含量要求元素允許含量%一般用途深沖鋼和特殊用途鋼Cu0.250.10Sn0.050.015Sb0.005As0.010Pb0.014~0.0021Bi0.0001~0.00015Ni0.100固態(tài)廢鋼的預(yù)處理技術(shù)有哪些?固態(tài)廢鋼的預(yù)處理技術(shù)。固態(tài)廢鋼的預(yù)處理主要是降低或者消除殘余有害元素不利影響的有效手段,常用的處理技術(shù)主要有機(jī)械挑選法。目前主要是依靠廢鋼回收部門的人工挑選,依靠有色金屬的比重,使用的類型加以挑選分類。目前一種廢鋼自動(dòng)化顏色識(shí)別系統(tǒng)已經(jīng)產(chǎn)生,該系統(tǒng)把破碎后的廢鋼由皮帶運(yùn)輸機(jī)運(yùn)送到識(shí)別系統(tǒng),由計(jì)算機(jī)進(jìn)行感光性和色澤的識(shí)別后,在特定的區(qū)域,由機(jī)械手或者氣缸把廢鋼推到指定的區(qū)域堆放,達(dá)到去除的目的。含銅廢鋼的冷凍處理。這種手段主要是利用液氮把含銅的廢鋼冷凍破碎后達(dá)到分離的目的。其優(yōu)點(diǎn)是去除有色金屬的工作的效率高,缺點(diǎn)是投資較大。硫化渣法脫銅。這是世界上研究最多的脫銅方法。主要原理是利用在600度以上的鐵液里,Cu2S比FeS穩(wěn)定,采用硫化鈉做渣料,促使鋼中的硫化銅向渣液轉(zhuǎn)移達(dá)到去除的目的。是一種成熟的技術(shù)。在沒有廢鋼處理設(shè)備的廢鋼里,常見的有害元素含量較高的廢鋼有:報(bào)廢的電機(jī)馬達(dá),汽車電瓶,軸承,易拉罐壓塊等。電爐煉鋼對(duì)于放射性廢鋼的要求.有哪些?隨著冷戰(zhàn)結(jié)束,前華約和北約在冷戰(zhàn)期間大量的核爆破試驗(yàn)用的車輛,坦克等效應(yīng)物,以及核電站,核設(shè)施使用過的報(bào)廢鋼鐵原料,隨著不同的渠道會(huì)進(jìn)入不同的市場,所以在進(jìn)口廢鋼輻射劑量的監(jiān)測上一定要有過硬技術(shù)裝備和值得信賴的部門把握。我們熟悉的某一個(gè)口岸曾經(jīng)發(fā)生過廢鋼的輻射劑量嚴(yán)重超標(biāo),為了消除輻射的影響,把堆放廢鋼場地地下一米厚的土鏟起后運(yùn)走深埋處理的事故。電爐廢鋼中間的硅含量高有何危害?硅含量較高,吹煉以后渣中的二氧化硅含量高,渣料石灰的消耗就會(huì)增加,吹氧時(shí)間相應(yīng)的延長,造成冶煉的各種難度增加。什么叫做高錳鋼,配料中間如何區(qū)分?錳含量高于8%的廢鋼稱為高錳鋼,高錳鋼的一個(gè)典型的特點(diǎn)是電磁盤吸不起來,只能夠使用廢鋼抓斗子配加,生產(chǎn)過程中可以利用此特點(diǎn)區(qū)分。電爐煉鋼對(duì)于高錳鋼廢鋼的加入量有哪些要求?目前高錳鋼廢鋼的循環(huán)量處在一個(gè)上升的時(shí)期,包括各種履帶車量的履帶,耐磨鑄球,碳素工具廢鋼等。由于高錳廢鋼中帶入的錳含量較高,所以會(huì)增加冶煉中脫磷脫碳的難度,影響冶煉的進(jìn)程,所以高錳廢鋼應(yīng)該分類堆放后,均勻的小批量加入,以消除高錳帶來的影響。電爐對(duì)于一些高硫廢鋼的加入要求有哪些?電爐流程冶煉的一個(gè)顯著特點(diǎn)是:電爐出鋼時(shí)和精練工序具有較強(qiáng)的脫硫能力,但是配入一些硫含量特別高的廢鋼,會(huì)導(dǎo)致鋼中的硫含量特別的高,導(dǎo)致精煉爐冶煉時(shí)間延長,冶煉成本超過了企業(yè)承受的底線。所以高硫廢鋼的配入應(yīng)該考慮到綜合平衡,使粗煉鋼水的硫控制在一個(gè)合理的水平很重要。硫特別高的廢鋼主要有以下幾種:制藥廠的一些鍋爐蒸餾器的管道,一些機(jī)械廠的切削碎屑,使用過的鑄鐵暖氣片,部分報(bào)廢的生鐵,耐候鋼板等。在使用這類廢鋼時(shí)要慎重,要考慮使用大量優(yōu)質(zhì)低硫的廢鋼,少量的配入此類廢鋼,達(dá)到“稀釋原料中硫含量”的目的。橡膠工業(yè)用硫或使橡膠硫化以改變生橡膠熱發(fā)黏冷變硬的不良性能,故含有橡膠的輪胎等物品必須挑揀出去。電爐煉鋼對(duì)于一些高磷廢鋼的加入有何要求?與高硫廢鋼相比,高磷廢鋼的配加也要考慮到對(duì)于冶煉成分控制的影響,以及對(duì)于冶煉成本的影響,做到全面平衡。一些高磷廢鋼的使用,也要依靠使用多數(shù)優(yōu)質(zhì)低磷廢鋼與之搭配使用,達(dá)到“稀釋”的目的,我們在生產(chǎn)中由于對(duì)于廢鋼搭配的不重視,發(fā)生過這樣的事故:冶煉普通鋼時(shí),對(duì)于脫磷的要求也不高,加上由于一直使用優(yōu)質(zhì)的低磷廢鋼,所以沒有發(fā)生過脫磷的矛盾。一次由于配入的磷過高,粗煉鋼水溫度和碳的成分合適后,煉鋼工只是注意了成分中的[C]和[Mn],忽略了磷,把[P]的成分0.07%認(rèn)為是0.007%出鋼后造成了廢品。所以高磷廢鋼的使用,特別是以下幾種的廢鋼尤其要注意:一些焊管,鑄件、易切削鋼的碎屑,廢的炮彈皮,油罐車的罐體,支架,低碳鍍錫鋼板,一些民營的小高爐冶煉的鑄造鐵。電爐對(duì)于廢鋼尺寸的要求有哪些?由于大塊廢鋼難熔,會(huì)影響吹氧操作,造成吹氧過程的飛濺和氧氣射流的反射,增加冶煉過程中的操作難度。為了熔化這些大塊廢鋼,需要提高熔池的溫度,而且大塊廢鋼在加料過程中會(huì)對(duì)爐襯產(chǎn)生沖擊。此外大塊廢鋼在穿井過程中砸斷電極也是冶煉中常見的事故之一。所以電爐冶煉用廢鋼的尺寸有嚴(yán)格的要求,不同廠家電爐公稱容量不同,要求也各有不同,但是50~120噸容量的電爐,要求如下:廢鋼堆密度應(yīng)大于0.7t/m3。最大長度不超過1.2m,最大斷面小于500mm×500mm,最大單重不超過500Kg。為了便于配料,各種類型的廢鋼應(yīng)分類堆放。中型廢鋼鐵的料型及尺寸要求有哪些?中型廢鋼鐵的料型及尺寸要求見下表類型外形尺寸(mm)含渣、土量典型舉例中型1類一級(jí)厚度≥10≤1.5%報(bào)廢的鋼錠、鋼坯、初軋坯、切頭、切尾、鑄鋼件、鋼軋輥、重型機(jī)械零件、切割結(jié)構(gòu)件、車軸、鋼軌、管材、船板、火車輪、工業(yè)設(shè)備等。方圓狀及圓柱實(shí)心體:Φ≥20二級(jí)厚度≥101.5%﹤含量≤4%方圓狀及圓柱實(shí)心體:Φ≥20三級(jí)厚度≥104%<含量≤7%方圓狀及圓柱實(shí)心體:Φ≥20四級(jí)厚度≥107%<含量≤10%方圓狀及圓柱實(shí)心體:Φ≥20五級(jí)厚度≥10含量﹥10%方圓狀及圓柱實(shí)心體:Φ≥202類一級(jí)6≤厚度<10≤1.5%軋廢的鋼坯及鋼材、車船板、機(jī)械廢鋼件、機(jī)械零部件、切割結(jié)構(gòu)件、火車軸、鋼軌、管材、廢舊工業(yè)設(shè)備等。方圓狀及圓柱實(shí)心體:12≤Φ<20二級(jí)6≤厚度<101.5%﹤含量≤4%方圓狀及圓柱實(shí)心體:12≤Φ<20三級(jí)6≤厚度<104%<含量≤7%方圓狀及圓柱實(shí)心體:12≤Φ<20四級(jí)6≤厚度<107%<含量≤10%方圓狀及圓柱實(shí)心體:12≤Φ<20五級(jí)6≤厚度<10含量﹥10%方圓狀及圓柱實(shí)心體:12≤Φ<20統(tǒng)料和輕薄料的技術(shù)要求和標(biāo)準(zhǔn)有哪些?統(tǒng)料的技術(shù)要求和標(biāo)準(zhǔn)見下表類型外形尺寸(mm)含渣、土量典型舉例統(tǒng)料1類一級(jí)4≤厚度<6≤1.5%機(jī)械廢鋼件、機(jī)械零部件、車船板、廢舊設(shè)備、汽車破碎料、鋼管、帶鋼、邊角余料等。方圓狀及圓柱實(shí)心體:8≤Φ<12二級(jí)4≤厚度<61.5%﹤含量≤4%方圓狀及圓柱實(shí)心體:8≤Φ<12三級(jí)4≤厚度<64%<含量≤7%方圓狀及圓柱實(shí)心體:8≤Φ<12四級(jí)4≤厚度<67%<含量≤10%方圓狀及圓柱實(shí)心體:8≤Φ<12五級(jí)4≤厚度<6含量﹥10%方圓狀及圓柱實(shí)心體:8≤Φ<122類一級(jí)2≤厚度<4≤1.5%機(jī)械廢鋼件、機(jī)械零部件、車船板、廢舊設(shè)備、汽車破碎料、鋼管、帶鋼、邊角余料等。方圓狀及圓柱實(shí)心體:4≤Φ<8二級(jí)2≤厚度<41.5%﹤含量≤4%方圓狀及圓柱實(shí)心體:4≤Φ<8三級(jí)2≤厚度<44%<含量≤7%方圓狀及圓柱實(shí)心體:4≤Φ<8四級(jí)2≤厚度<47%<含量≤10%方圓狀及圓柱實(shí)心體:4≤Φ<8五級(jí)2≤厚度<4含量﹥10%方圓狀及圓柱實(shí)心體:4≤Φ<8輕薄料的技術(shù)標(biāo)準(zhǔn)和要求如下表類型外形尺寸(mm)含渣、土量典型舉例輕薄料一級(jí)厚度:<2≤1.5%薄板、切邊、化工廢鋼、容器、醫(yī)療器械、直徑不大于4.0mm盤條和鋼絲等方圓狀圓柱實(shí)心體:Φ<4二級(jí)厚度:<21.5%﹤含量≤4%方圓狀及圓柱實(shí)心體:Φ<4三級(jí)厚度:<24%<含量≤7%方圓狀及圓柱實(shí)心體:Φ<4四級(jí)厚度:<27%<含量≤10%方圓狀及圓柱實(shí)心體:Φ<4五級(jí)厚度:<2含量﹥10%方圓狀及圓柱實(shí)心體:Φ<4增碳劑的技術(shù)要求有哪些?常用的增碳劑成分要求見下表牌號(hào)固定碳(%)灰份揮發(fā)份硫(%)水份粒度一級(jí)二級(jí)C-9089.5~90.5<6%<2.0%≤0.30.3~0.5<0.5%2~6mmC-91>90.5C-92>91.5C-93>92.5C-7570.0~75.0——噴吹碳粉85.0~90.0<6%<2.0%≤0.30.3~0.5<0.5%<1mm什么叫做直接還原鐵?電爐煉鋼使用的直接還原鐵是怎樣生產(chǎn)出來的?直接還原是指在礦石不熔化、不造渣的條件下將鐵的氧化物還原為金屬鐵的工藝方法。這種方法用煙煤或天然氣作還原劑,不用焦碳,不用龐大的高爐。直接還原是在固態(tài)溫度下進(jìn)行,所得的產(chǎn)品稱為直接還原鐵DRI(DirectReductionIron)。目前直接還原法主要有氣基直接還原法和煤基直接還原法兩大類。直接還原鐵的金屬化率均在90%左右。直接還原鐵由過去的海綿鐵(spongeIron)發(fā)展為現(xiàn)在的粒狀直接還原鐵(DIR)以及塊狀的熱壓塊HBI,由于直接還原鐵中金屬鐵的含量較高,而且硫和磷的含量比較低,所以是電爐生產(chǎn)純凈鋼的重要鋼鐵原料的替代品。目前全世界的直接還原鐵的總產(chǎn)量占生鐵產(chǎn)量的6%~9.4%,在3000萬到6000萬左右,氣基生產(chǎn)直接還原鐵的技術(shù)和產(chǎn)量都占主導(dǎo)地位,氣基生產(chǎn)法主要有:Midrex法,HYL法,Fior法,煤基生產(chǎn)法主要有:回轉(zhuǎn)窯法包括SL/RNI,Krup法Corex法,DRC法,ACCAR法。正在開發(fā)的煤基法有Inmetco法,Fastmet法,Comet法以及finmet法〔1〕。其中豎爐法生產(chǎn)的DRI是優(yōu)質(zhì)廢鋼的替代用品,是用來生產(chǎn)優(yōu)質(zhì)鋼種的理想原料。一般的直接還原鐵的理化指標(biāo)和形狀有哪些?直接還原鐵其主要的理化指標(biāo)見下表組成元素含量%組成的化學(xué)成分含量%全鐵90~93SiO21~3金屬鐵80~86A12030.5~2金屬化率90~94脈石(A1203SiO2CaOMgO)2.7~5C0.2~1.4S0.01~0.04殘余元素的總量0.015~0.04P0.04~0.07堆密度2.7~2.9直接還原鐵有三種外觀形狀塊狀。塊礦在豎爐或回轉(zhuǎn)窯內(nèi)直接還原得到的海綿狀金屬鐵。金屬化球團(tuán)。使用精礦粉先造球,干燥后在豎爐或回轉(zhuǎn)窯中直接還原得到的保持球團(tuán)外形的直接還原鐵。熱壓塊鐵HBI。把剛剛還原出來的海綿鐵或金屬球團(tuán)趁熱加壓成型,使其成為具有一定尺寸的鐵塊,一般尺寸多為100mm×50mm×30mm,其密度一般高于海綿鐵與金屬化球團(tuán)。HBI的表面積小于海綿鐵與金屬化球團(tuán),使其在保管或運(yùn)輸過程中不易發(fā)生氧化,在電爐中使用時(shí)裝料的效率高。電爐煉鋼對(duì)于直接還原鐵的性能要求有哪些由于電爐煉鋼的特殊性,所以對(duì)于直接還原鐵有一定的要求,一般要求如下:(1)密度要在4.0~6.5g/cm3之間。(2)一般要求冷態(tài)條件下抗拉強(qiáng)度大于70Mpa,以保證運(yùn)輸和加料過程中不易破碎。(3)要求粒度合適。既不能含過量的粉塵,也不能尺寸過大,使其能避免氧化或被電爐除塵裝置吸收,又能適于爐頂連續(xù)加料的要求。一般粒度要求在10~100mm之間。直接還原鐵的實(shí)體照片見下圖。(4)要求直接還原鐵中雜質(zhì)含量不能過高,尤其是指脈石的含量。脈石的含量過高,會(huì)導(dǎo)致造渣的石灰量加大,不利于節(jié)電和提高技術(shù)回收率。圖:煤基直接還原鐵的實(shí)體照片圖:FINMET工藝生產(chǎn)的熱壓塊實(shí)體照片(5)要求金屬化率不能太低(金屬化率是直接還原鐵中金屬鐵與總鐵的百分比),金屬化越低,則直接還原鐵中的氧化鐵越高,理論上DRI每增加1%,需要10.4KWh/t的電能還原氧化鐵,而且會(huì)影響冶煉鋼水的金屬總收得率。直接還原鐵如何加入?直接還原鐵的密度介于爐渣(2.5~3.5g/cm3)與鋼液(7.0g/cm3)之間。加入爐內(nèi)后容易停留在渣-鋼界面上,有利于鋼渣界面的脫碳反應(yīng),促進(jìn)爐內(nèi)傳熱的進(jìn)行。直接還原鐵用于電弧爐煉鋼,其中金屬化率和含碳量不同,所以加入量也不相同。對(duì)于碳含量和金屬化率較高的直接還原鐵,可以100%的作為電爐煉鋼的廢鋼爐料。如果所用的直接還原鐵的加入比例為30%以下,則可用料罐加入。料罐的底部裝輕廢鋼,隨后裝入重廢鋼和DRI,這樣可避免DRI結(jié)塊太多。DRI主要裝在料罐的下半部,使DRI盡可能裝入爐內(nèi)中心部位,防止直接還原鐵接近爐壁以及冷區(qū)結(jié)塊而不能熔化。由一種情況需要注意的是:當(dāng)電弧從上部加熱相當(dāng)厚的DRI料層時(shí),熔化的金屬便充填各個(gè)DRI球團(tuán)之間的空隙并凝結(jié),不能滲入到球團(tuán)深部,球團(tuán)易燒結(jié)在一起而且密度小,難以落入鋼水中,延長了熔化時(shí)間。實(shí)踐表明,成批加入大于總爐料的30%的DRI時(shí),由于DRI傳熱慢,會(huì)出現(xiàn)難以熔化的問題,惡化其經(jīng)濟(jì)技術(shù)指標(biāo),使用連續(xù)加料技術(shù),會(huì)改善這種情況。連續(xù)加料一般從爐頂?shù)募恿峡准尤?。一是在爐頂?shù)膸缀沃行拈_一個(gè)加料孔,使DRI垂直落入;另一種方式是在爐頂半徑的中間開孔,經(jīng)軌道拋射落入爐內(nèi)的中心區(qū)域。爐頂上部的連續(xù)加料系統(tǒng)必須有足夠的高度,以保證DRI具有足夠的動(dòng)能以快速穿過渣層。由于一般的直接還原鐵的含碳量比較低,不利于熔池的盡快形成。氣基還原鐵能較好控制DRI中的碳含量,一般可作到其中的碳與未還原的FeO相平衡,即所謂“平衡的DRI”。冶煉時(shí)無需額外配碳,DRI也不會(huì)向熔池增碳;對(duì)于煤基還原的DRI,一般碳含量在0.25%左右,冶煉時(shí)需配入一定的碳(根據(jù)DRI金屬化率和所煉鋼種而定),以保證熔池合適的碳含量并使DRI中的FeO還原。直接還原鐵配加鐵水的操作要點(diǎn)有哪些?我們在生產(chǎn)實(shí)踐中經(jīng)過大量的實(shí)踐證明,含碳量較低的直接還原鐵,全廢鋼冶煉中使用效果不理想,在配加鐵水的生產(chǎn)中取得的效果是比較理想的。基本操作要點(diǎn)作如下:不同產(chǎn)地的直接還原鐵中脈石含量不同,大量使用時(shí)要注意渣料石灰的加入量,避免爐渣堿度低造成冶煉過程的脫磷化學(xué)反應(yīng)不能達(dá)到成分控制的要求。熱裝鐵水冶煉時(shí),直接還原鐵在第一批料隨廢鋼鐵料一起加入,并且采用較大的留鋼量,對(duì)于優(yōu)化脫碳脫磷操作十分有利。使用直接還原鐵要注意提高入爐料的配碳量,如果配碳量不足,會(huì)造成直接還原鐵形成冷區(qū),不容易熔化。由于碳可以降低鐵素體的熔點(diǎn),合適的配碳量,會(huì)幫助熔池盡快形成,有利于消除直接還原鐵的大塊凝固現(xiàn)象。一般情況下,直接還原鐵加入量在20%~30%,配碳量保持在1.2%~1.8%,低于20%的直接還原鐵,配碳量控制在0.8%~1.5%之間是合適的。這種方式有利于爐渣的早期形成和促進(jìn)脫碳反應(yīng)的速度,脫〔P〕效果好,縮短了冶煉時(shí)間。原因是直接還原鐵中的氧化鐵促進(jìn)了石灰的早期熔解和增加了渣中氧化鐵的含量。實(shí)踐中鐵水加入比例與直接還原鐵加入比例的最佳比例為3.5/2。熱裝鐵水配加直接還原鐵冶煉時(shí),盡可能的使用最大的功率送電,有熔池形成時(shí)就進(jìn)行噴碳操作,促使泡沫渣埋弧冶煉,盡快提高熔池的溫度。吹氧冶煉期間,要注意吹氧的操作和送電的操作,從爐門放渣的時(shí)間要盡量晚一些,脫碳反應(yīng)開始以后,要來回間歇性的傾動(dòng)爐體,利用脫碳反應(yīng)的動(dòng)力促使熔池內(nèi)部的冷區(qū)消融。冶煉過程中,鐵水的比例小于20%,直接還原鐵的加入量在10%~30%之間,冶煉的電耗將會(huì)增加15Kwh/t~50Kwh/t,所以鐵水加入比例較小時(shí),直接還原鐵的裝入量要偏下限,以便于快速提溫和縮短冶煉周期。熱裝鐵水的比例大于30%以后,裝入量控制在中上限,有利于增加臺(tái)時(shí)產(chǎn)量。作為生鐵配碳冶煉時(shí)有哪些特點(diǎn)?(1)冷生鐵的導(dǎo)熱性不好,所以加入時(shí)要注意盡量避免加在爐門和出鋼口附近,給冶煉操作帶來困難。配料時(shí)生鐵的加入應(yīng)該加在料籃的中下部最為合理,這樣可以利用生鐵含碳量較高的優(yōu)點(diǎn),及早形成熔池,不僅有利于提高吹氧的效率,而且會(huì)提高金屬收得率。如果加在爐門區(qū),一是加料后堆積在爐門區(qū)的冷生鐵,很有可能從爐門區(qū)掉入渣坑,造成浪費(fèi)。二是影響了從爐門區(qū)的吹氧操作。三是會(huì)影響取樣操作,或者取樣的成分沒有代表性。加在出鋼口區(qū),會(huì)發(fā)生堵塞出鋼口的事故,或者出鋼時(shí),未熔解的生鐵在等待出鋼的時(shí)間和出鋼過程的這段時(shí)間內(nèi)發(fā)生熔解以后,導(dǎo)致出鋼增碳現(xiàn)象,引起成分出格的事故。(2)一般來講冷生鐵的配入量在裝入量的20%~65%之間,自耗式氧槍吹煉方式下的配加比例為20%~45%,冶煉低碳鋼取中下限,冶煉中高碳鋼取中上限。超音速氧槍吹煉模式下的的冷生鐵的加入量在40%~65%之間,具體的比例可以根據(jù)與之搭配廢鋼的條件來定。超音速集束氧槍吹煉條件下的配加比例最多可以增加到70%。我們的統(tǒng)計(jì)表明,生鐵加入量在超過40%以后,生鐵的比例每增加5%,金屬的回收率將會(huì)提高1%~1.6%,我們在超音速爐壁氧槍和爐門一枝自耗式氧槍復(fù)合吹煉條件下,生鐵配加廢鋼,生鐵的比例在60%時(shí),金屬總體收得率達(dá)到平均95%以上,冶煉時(shí)間沒有延長。(3)使用冷生鐵配碳冶煉優(yōu)質(zhì)鋼的爐次,在冷區(qū)會(huì)出現(xiàn)軟熔現(xiàn)象,即第一次取樣與第二次取樣的結(jié)果偏差較大,包括〔P〕[C],尤其是〔P〕。這種現(xiàn)象在自耗式氧槍吹煉的條件下尤其明顯。供氧強(qiáng)度較大的超音速氧槍或者超音速集束氧槍吹煉模式下,這種情況會(huì)有所好轉(zhuǎn)。所以用生鐵配碳冶煉時(shí),終點(diǎn)取樣溫度應(yīng)該在1580℃~1630℃之間。出鋼前從爐門仔細(xì)觀察爐內(nèi)是否有未熔解的冷廢鋼,是必需的。(4)加入加高比例的冷生鐵冶煉時(shí)候,保持爐內(nèi)的合適的留渣留鋼量是促進(jìn)冶煉優(yōu)化的關(guān)鍵操作。(5)有些生鐵含有較高的硅和磷,在加入生鐵比例較高的冶煉爐次,要根據(jù)生鐵的成分合理的配加渣料石灰,防止冶煉過程出現(xiàn)磷高和頻繁的沸騰現(xiàn)象。筆者多次在實(shí)際操作中遇到這種現(xiàn)象:在石灰稱量秤誤差較大時(shí),因?yàn)槭壹尤肓坎粔颍霈F(xiàn)過磷高的事故,而且冶煉中隨著脫碳反應(yīng)和冷生鐵的不斷熔解,爐內(nèi)不斷發(fā)生劇烈沸騰,從爐門溢出鋼水的事故,經(jīng)過后來的化驗(yàn)分析證實(shí),這是由于加入的冷生鐵硅含量和磷含量嚴(yán)重超標(biāo),石灰加入量的偏差較大造成的。(6)冷生鐵表面具有許多不平的微小孔洞和半貫穿性的氣孔,有利于脫碳反應(yīng)的一氧化碳?xì)馀莸男纬?,有利于脫碳反?yīng)的進(jìn)行。在廢鋼資源緊張的地區(qū),利用鐵水和冷生鐵一起配碳,不會(huì)延長脫碳的時(shí)間和冶煉周期。其中鐵水占30%,生鐵占35%的比例搭配,在實(shí)際操作中的效果最佳。直接還原鐵配加生鐵冶煉的操作要點(diǎn)有哪些?全廢鋼冶煉時(shí),直接還原鐵的加入量要控制在30%以內(nèi),最佳的加入量要根據(jù)熔池的配碳量來決定。配碳量加大時(shí),直接還原鐵的加入比例可以大一點(diǎn),反之亦然。電爐的留鋼量要偏大一些,直接還原鐵的加入不能加在爐門區(qū)和EBT冷區(qū)。料籃布料時(shí),廢鋼首先加在爐底,再加直接還原鐵,當(dāng)直接還原鐵加入量較大時(shí),應(yīng)該分兩批加入。加入廢鋼鐵料的配碳量要控制在1.2%~2.0%。爐渣的二元堿度要保持在2.0~2.5之間。裝入量要控制在公稱裝入量的中限以下,以利于熔池快速提溫。冶煉過程中,在有熔池形成時(shí),就要考慮進(jìn)行噴碳操作,以降解渣中的氧化鐵含量,營造良好的泡沫渣埋弧冶煉。在有脫碳反應(yīng)征兆出現(xiàn)時(shí),可以根據(jù)冶煉的進(jìn)程調(diào)節(jié)噴碳的速度。直接還原鐵容易在爐壁冷區(qū)和熔池靠近EBT出鋼口的附近沉積,在脫碳量不大,熔池溫度較低時(shí),形成難熔的“冰山”,所以出鋼溫度要保持在1620℃~1650℃之間,出鋼前還要仔細(xì)觀察爐內(nèi)的情況,防止冷區(qū)的存在引發(fā)事故。在沒有附助能源輸入的時(shí)候,或者熔池升溫速度較慢的階段,最好少加或者不加直接還原鐵。主要是因?yàn)橐睙掃^程中熔池溫度較低時(shí),碳氧反應(yīng)開始的較晚,低溫階段鐵會(huì)大量氧化加入渣中,在渣中富集以后流失,增加了鐵耗,在熔池溫度升高以后還有可能導(dǎo)致大沸騰事故的發(fā)生。電爐使用直接還原鐵對(duì)于電耗的影響如何?碳含量較低的直接還原鐵使用后冶煉電耗有增加的趨勢,這種趨勢是隨著入爐料的配碳量和直接還原鐵的加入量動(dòng)態(tài)波動(dòng)的,直接還原鐵加入量超過25%以后,增加的電耗比較明顯。氣基生產(chǎn)的直接還原鐵,含碳量較高,脫碳反應(yīng)的熱效應(yīng)會(huì)減少冶煉電耗的上升。電爐使用直接還原鐵對(duì)于金屬收得率的影響如何?配加直接還原鐵以后,爐料的配碳量決定了直接還原鐵的金屬收得率。通過提高熔池的配碳量,實(shí)行多點(diǎn)噴碳,增加碳氧槍噴吹碳粉的數(shù)量來調(diào)整鋼渣中的氧化鐵含量,促進(jìn)直接還原鐵中的氧化鐵的還原進(jìn)入鋼液,是提高金屬收得率的有效方法。利用直接還原鐵配加高比例的熱裝鐵水,可以顯著提高金屬的收得率。對(duì)于渣料的影響實(shí)際上直接還原鐵帶入的脈石與廢鋼帶入的雜質(zhì)含量是差不多的,有時(shí)候甚至比廢鋼帶入的要低。所以配加直接還原鐵以后,對(duì)于渣料的影響不大,直接還原鐵的加入比例在30%以內(nèi),渣料的加入量不會(huì)顯著上升,有時(shí)候還可以有所下降。加入直接還原鐵對(duì)于冶煉周期和電極的消耗的影響如何?對(duì)于全廢鋼冶來講,配加直接還原鐵,由于電耗有所增加,通電時(shí)間延長,冶煉周期也隨之增加。熱裝鐵水冶煉的時(shí)候,鐵水比例大于30%以上時(shí),由于直接還原鐵的加入會(huì)提高脫碳速度,控制好送電曲線,冶煉周期不會(huì)明顯增加,有時(shí)候還會(huì)有所下降。鐵水加入比例低于20%時(shí),冶煉周期取決于裝入量和配碳量。總體的統(tǒng)計(jì)表明,熱裝鐵水冶煉時(shí),配加12%~30%的DRI,一般可使一爐鋼的冶煉時(shí)間縮短3~5min。對(duì)于電極消耗的影響。此外配加直接還原鐵冶煉時(shí),電極的消耗有所上升。這主要是通電時(shí)間增加以后,增加了電極的消耗。電爐使用直接還原鐵對(duì)于脫碳和氧耗的影響如何?配加直接還原鐵以后,由于直接還原鐵帶入一定量的氧化鐵會(huì)促進(jìn)爐渣的熔化,提高脫碳速度,冶煉的氧耗有所下降,下降的值在0.5m3/t~3.53/t.加入直接還原鐵對(duì)于鋼的質(zhì)量的影響如何?配加直接還原鐵以后,鋼中有害元素的含量,特別是重金屬元素Ni、Cr、Mo、Cu、Sn的含量會(huì)有所下降,有利于提高鋼水的潔凈度,同時(shí)直接還原鐵中的氣體含量也比較低,配加直接還原鐵以后,泡沫渣的控制在一定的程度上比較容易控制,脫碳反應(yīng)也能夠比較順利的進(jìn)行,對(duì)于降低鋼中的氣體含量比較有利。加入直接還原鐵以后,對(duì)于廢鋼中有害元素的稀釋作用見下圖圖:直接還原鐵加入后對(duì)于有害元素的影響直接還原鐵的理論密度如何計(jì)算?直接還原鐵的理論密度可以按照下式計(jì)算[4](1)式中ρσ:直接還原鐵的理論計(jì)算密度ρi:組分的密度αi:組分的百分含量,%其中典型的熱壓快,供貨粒度為50×100mm,按照組分的質(zhì)量含量計(jì)算比重的方法見下式(2)理論計(jì)算的比重在6.1~6.5t/m3之間,與實(shí)物的比重接近直接還原鐵的理論金屬收到率如何計(jì)算?直接還原鐵的理論金屬收得率計(jì)算公式表示為]:(4)式中SiO2%、P%、S%、Mn%:各個(gè)組分的質(zhì)量百分?jǐn)?shù)∑пi:其余的雜質(zhì)成分的百分?jǐn)?shù)計(jì)算結(jié)果表明,各類直接還原鐵的金屬收得率的范圍在86%~92%之間。加入直接還原鐵對(duì)于冶煉安全有影響嗎?直接還原鐵含碳量較低,金屬化率較低的直接還原鐵使用過量后,由于氧化鐵在渣中容易富集,操作不當(dāng)會(huì)引發(fā)熔池大沸騰的惡性事故。同時(shí)直接還原鐵容易形成難熔的“冰山”,操作不當(dāng)時(shí),會(huì)發(fā)生出鋼時(shí)堵塞出鋼口,出鋼量得不到保證的事故。冷生鐵有哪些特點(diǎn)?生鐵塊的熔點(diǎn)低于廢鋼,比熱容大于廢鋼,兩者的熔化熱大致相等(1.35MJ/kg)。作為電爐煉鋼的原料,是一種優(yōu)質(zhì)的煉鋼原料,其基本大概成分見下表成分金屬鐵CPSMnSi含量%〉933.8~4.2《0.08《0.60.2~0.4《1.0冷生鐵的配碳量如何計(jì)算?冷生鐵和鐵水帶入的配碳量可以由下式確定:C%=Q·α·100%/G式中:C%:生鐵或者鐵水帶來的配碳量Q:生鐵或鐵水加入量α:生鐵或鐵水的碳含量G:加入的廢鋼鐵料的總量什么叫做碳化鐵(Fe3C)?碳化鐵(Fe3C)也是氣基直接還原鐵的一種半工業(yè)化的實(shí)驗(yàn)產(chǎn)品,其工藝是通過氣體-固體的反應(yīng),將鐵礦粉轉(zhuǎn)變?yōu)樘蓟F的閉環(huán)吸熱的一步式工藝。經(jīng)過處理的氣流(CO,CO2,H2,CH4,水蒸氣)在550℃~600℃下與0.1~1.0mm的鐵礦粉反應(yīng)生成碳化鐵。由于碳化鐵由于具有較高的化學(xué)潛熱,有害雜質(zhì)含量很低,被認(rèn)為是一種最有潛力的電爐煉鋼原料的替代品,由于規(guī)?;a(chǎn)的技術(shù)問題與資源礦產(chǎn)的制約,所以目前沒有形成規(guī)?;纳a(chǎn),但是對(duì)于它的實(shí)驗(yàn)性使用和工業(yè)性應(yīng)用,已經(jīng)有了大量的文獻(xiàn)報(bào)道。典型的碳化鐵成分見表4-4〔7〕表4-4:典型的碳化鐵的成分成分總鐵金屬鐵Fe3CFe3O4SiO2PS含量%89~940.5~188~942~72~3<0.035<0.01電爐煉鋼對(duì)于碳化鐵的要求有哪些?金屬化率要高。由于碳化鐵中的Fe3O4與碳反應(yīng)為還原吸熱反應(yīng),當(dāng)碳化鐵中Fe3O4的含量超過19%,將會(huì)是一個(gè)負(fù)的熱效應(yīng)。所以電爐使用的碳化鐵的金屬化率要盡可能的高。我們在生產(chǎn)中做的實(shí)驗(yàn)表明:還原1t的氧化鐵,需要電能1~4MWh的電能。碳化鐵中的酸性物質(zhì)脈石的含量要低,避免帶入爐內(nèi)酸性物質(zhì)過多,增加石灰的用量。由于碳化鐵的硬度較大,所以電爐使用時(shí),粒度和塊度要適當(dāng),用于料籃加入的,要和生鐵的塊度差不多,用于噴吹的,粒度要滿足噴吹的需要。碳化鐵的加入方式有哪幾種方式?碳化鐵可以將其在熱態(tài)下壓塊,或者?;?,通過料籃向電弧爐中加入,也可采用爐頂?shù)谒目谆蛘叩谖蹇准尤?。采用料籃加入時(shí),加入方式可以和加生鐵的方式差不多,加在料籃底部或者中下部。由于碳化鐵堅(jiān)硬,無粘性,流動(dòng)性好,如果采用豎井預(yù)熱后加入或者噴吹加入,效果會(huì)更好,在采用豎井加入時(shí),發(fā)生碳化鐵過熱以后粘手指的現(xiàn)象會(huì)較少。采用爐頂?shù)谒目谆蛘叩谖蹇准尤敕绞剑尤氲撵`活性會(huì)更大,不會(huì)在加料過程中發(fā)生由于粘結(jié)造成的管道堵塞。加入可在冶煉過程中進(jìn)行而不必中斷冶煉,能夠縮短冶煉時(shí)間,還可以減少熱損失,提高熱效率。采用噴吹加入,則噴吹速度要控制合適。什么叫做脫碳粒鐵?如何生產(chǎn)的?脫碳粒鐵是一種生產(chǎn)工藝已經(jīng)實(shí)驗(yàn)成功,并且在30t和150t電爐上實(shí)驗(yàn)過的新型電爐煉鋼原料,脫碳粒鐵的生產(chǎn)流程見下圖1:高爐2:水池3:料倉4:回轉(zhuǎn)窯5:粒鐵罐6:除塵設(shè)施7:皮帶輸送機(jī)8:高壓水9:鐵水10:風(fēng)機(jī)11:高爐爐頂煤氣其主要的生產(chǎn)流程是:先將煉鋼生鐵用高壓水沖制成3~15㎜的粒鐵,粒鐵的粒度可以通過控制高壓水的壓力和流量來進(jìn)行控制,然后把粒鐵裝入回轉(zhuǎn)窯中進(jìn)行固態(tài)脫碳。如上圖所示,粒鐵由窯尾的給料裝置連續(xù)均勻的加入窯內(nèi),依靠窯頭的高爐煤氣和粒鐵脫碳后的產(chǎn)物CO燃燒所放出的熱量來加熱粒鐵,脫碳使用的氧化劑為高爐的尾氣和隧道窯的尾氣CO2,粒鐵里的碳含量可以隨機(jī)控制,可以控制在0.2%~2.0%之間,有害元素含量低,與直接還原鐵相比,粒鐵沒有脈石,可以減少煉鋼的渣料,降低電耗;堆比重比較大,可以減少加料次數(shù),電弧爐可以實(shí)現(xiàn)熱裝,是一種冶煉高級(jí)質(zhì)量的優(yōu)質(zhì)煉鋼原料。脫碳粒鐵的主要成分見下表表:脫碳粒鐵的成分與理化指標(biāo)化學(xué)成分%物理性能CSiPSFeOCuNi+C粒度/mm密度/t*m-3<1.50.6<0.05<0.04<5<0.01<0.0075~153.5~4.0根據(jù)以上介紹,我們可以知道,作為電爐新鐵料的一種,脫碳粒鐵可以根據(jù)脫碳粒鐵的碳含量,決定加入量,加入量可以在30%~100%。加在料籃底部對(duì)于減少加料對(duì)于爐底的沖擊,調(diào)整吹氧操作對(duì)有好處,對(duì)于直流電爐來講,脫碳粒鐵更是一種理想的原料。什么叫做Corx鐵?Corx鐵是煉鐵工業(yè)的一種生產(chǎn)新方法,目前的報(bào)道證實(shí)這是一種可以工業(yè)化生產(chǎn)的煉鋼原料,使用與鐵水(或者冷生鐵)的原理大致相同。什么叫做鐵水熱裝技術(shù)?鐵水熱裝技術(shù)就是將鐵水加入電爐,作為鋼鐵原料的一種技術(shù)。熱裝鐵水是一項(xiàng)影響電爐冶煉歷史的新技術(shù),鐵水熱裝技術(shù)除了具有冷生鐵的相同的優(yōu)缺點(diǎn)外,還帶入了大量的物理熱,為縮短冶煉周期,強(qiáng)化冶煉創(chuàng)造了良好的條件。熱兌鐵水對(duì)于渣料的加入有何要求?電爐脫碳反應(yīng)的主要部分是經(jīng)過鋼渣界面進(jìn)行的,這一點(diǎn)在電爐熱兌鐵水的生產(chǎn)中也得到了充分的驗(yàn)證,爐渣的二元堿度低于1.5,電爐熱兌鐵水的冶煉狀況就會(huì)惡化。所以在增加鐵水熱兌比以后,渣料的加入量要根據(jù)鐵水中[P],[Si]含量,合理的調(diào)劑石灰的加入量,在沒有鐵水成分預(yù)報(bào)的情況下,石灰的加入量要比正常多20~25kg/t,以保證冶煉的正常進(jìn)行。零電耗冶煉的爐料結(jié)構(gòu)指什么?零電耗冶煉是指電爐熱兌鐵水比例大于65%以后,通過燒嘴或者氧槍的吹氧的冶金反應(yīng),輸入化學(xué)熱,再充分利用鐵水的物理熱和化學(xué)熱就可以將爐料加熱至熔化狀態(tài),繼而滿足煉鋼的冶金熱力學(xué)條件,使得繼續(xù)升溫達(dá)到出鋼溫度,不需要送電,或者只需要極小的一部分電能,這種冶煉工藝稱為零電耗電爐冶煉技術(shù)。什么叫做電爐爐料的三角形結(jié)構(gòu)?爐料結(jié)構(gòu)三角形的提出電弧爐煉鋼爐料結(jié)構(gòu)一般是指各種含鐵原料配入量在含鐵原料總配入量中所占的比例。如果含鐵原料為廢鋼(scrap)、生鐵(pig)和直接還原鐵(DRI),按傳統(tǒng)意義其爐料結(jié)構(gòu)參數(shù)為scrap,pig和DRI(其中scrap=Gscrap/(Gscrap+Gpig+GDRI)。Gscrap,Gpig,GDRI。分別為廢鋼、生鐵和直接還原鐵的配入量)。傳統(tǒng)方法分析爐料結(jié)構(gòu)中各參數(shù)對(duì)諸如噸鋼耗電、出鋼量、冶煉周期等主要技術(shù)經(jīng)濟(jì)指標(biāo)的影響,是將這三個(gè)因素分別討論,而這三個(gè)爐料結(jié)構(gòu)參數(shù)應(yīng)滿足總量為1(100%)的條件,實(shí)際上只有兩個(gè)獨(dú)立變量??梢?,按常規(guī)將三個(gè)參數(shù)scrap,pig和DRI作為爐料結(jié)構(gòu)參數(shù)在理論上是有缺陷的。為了更科學(xué)地描述三元爐料的結(jié)構(gòu),參照物理化學(xué)中三元相圖的濃度三角形的概念,引入了電弧爐煉鋼“爐料結(jié)構(gòu)三角形”(見圖)。圖中等邊三角形的三個(gè)頂點(diǎn)分別表示某一種原料(配入比例為100%),由此構(gòu)成的爐料結(jié)構(gòu)三角形具有與濃度三角形類似的性質(zhì)。稱為爐料的三角形結(jié)構(gòu)。自耗式氧槍吹煉條件下提高鐵水熱兌比例的方法有哪些?采用自耗式氧槍吹煉的電爐,由于自耗式氧槍的脫碳速度比較低,所以提高自耗式氧槍吹煉過程的脫碳速度是提高兌加鐵水比例的關(guān)鍵,主要的方法有:(1)適當(dāng)增大電爐的留鋼量和留渣量。兌入鐵水后氧槍伸入留鋼留渣與兌入鐵水組成的局部熔池吹氧脫[C],盡可能改變傳統(tǒng)的“氧槍割料”操作。在送電吹氧3min左右,局部熔池即可達(dá)到脫碳的溫度要求開始脫碳〔11〕,由此達(dá)到“塌料,熔清”70%~80%的廢鋼料,然后加料的目的。此操作方法可以使熔化期的脫[C]量占總配[C]量的40%以上,減輕了氧化期的脫[C]任務(wù)。(2)定期的修補(bǔ)爐底。由于脫碳反應(yīng)的產(chǎn)物一氧化碳?xì)馀?,它的形成在于爐壁和爐底的耐材表面,合理的熔池深度,有利于氧槍吹煉,能夠很容易的把氧氣噴吹在鋼渣界面,或者吹入鋼液內(nèi)部,有利于誘發(fā)脫碳反應(yīng)的開始,提高熔池脫碳反應(yīng)的活躍程度。此外,電爐熔池過深,不利于電爐熔池內(nèi)鋼液的“湍流”運(yùn)動(dòng),不利于鋼液內(nèi)部一氧化碳?xì)馀莸呐懦觯簿筒焕谠谂R界碳含量范圍內(nèi),鋼液內(nèi)部的碳,向鋼渣界面或者脫碳反應(yīng)區(qū)的擴(kuò)散和遷移。(3)提高爐渣的堿度。提高脫碳速度,首先要穩(wěn)定操作。將爐渣的堿度適當(dāng)提高(R≥2.0),電爐的廢鋼鐵料熔清大部分以后先化渣,成渣充分后,噴入適量碳粉用以擴(kuò)大鋼渣反應(yīng)界面,以促使脫[C]反應(yīng)盡早進(jìn)行。脫[C]反應(yīng)開始后,控制噴入發(fā)泡劑碳粉的量,以保證渣中(FeO)20%左右,以獲得較高的脫[C]速度,促進(jìn)熔化初期熔池?cái)噭?dòng)傳熱充分熔清。泡沫渣發(fā)泡氣源通過熔池脫碳反應(yīng)取得。這對(duì)于臨界碳濃度范圍內(nèi)的脫[C]很關(guān)鍵,也很有利。(4)提高供氧強(qiáng)度。一般來講,供氧強(qiáng)度越大,氧氣的利用率越高,脫碳速度也越快,增加供氧強(qiáng)度以后,相應(yīng)的可以增加鐵水的熱兌比例。如何提高超音速氧槍吹煉條件下鐵水熱兌比例?超音速氧槍具有較強(qiáng)的穿透鋼渣界面的能力,但是石灰熔解的速度較慢,爐渣參與傳質(zhì)的作用減小了,此外超音速氧槍極其容易造成爐渣,鋼水爐氣三相間的乳化,乳化現(xiàn)象一發(fā)生,就會(huì)導(dǎo)致鋼渣混合物從爐門溢出進(jìn)入渣坑,是造成脫碳困難和鐵耗高的主要原因。在某種程度上,脫碳速度比自耗式氧槍要快,但是超音速氧槍吹煉條件下的脫碳操作,受影響的因素比較多,而且會(huì)產(chǎn)生脫磷與脫碳不能兼顧優(yōu)化的矛盾,在熱兌鐵水生產(chǎn)時(shí),這種矛盾時(shí)常會(huì)更加突出。主要體現(xiàn)在以下方面:(1)超音速水冷氧槍脫碳具有一定的局限性。特別是在爐役中后期,爐底較深時(shí),由于超音速氧槍的槍位最低位置是固定的,所以射流穿透鋼渣的作用受到限制,鋼渣之間的界面反應(yīng)能力受到抑制,在臨界碳含量范圍內(nèi)容易造成“碳高”,部分爐次的氧化期吹煉過程中,會(huì)出現(xiàn)吹煉時(shí)沒有碳氧反應(yīng)的征兆-碳火的出現(xiàn),有的甚至出現(xiàn)了大沸騰事故。影響鐵水熱兌比例的提高。(2)超音速氧槍在熱兌鐵水吹煉時(shí),時(shí)常有爐壁粘結(jié)鋼渣現(xiàn)象嚴(yán)重,爐沿升高,影響爐蓋旋轉(zhuǎn),泡沫渣生成速度較慢的缺點(diǎn),部分爐次在堿度正常,脫磷效果不好的現(xiàn)象。這在一定程度上也影響了熱兌鐵水比例的提高。(3)脫碳困難時(shí),為了防止大沸騰現(xiàn)象,送電攪拌熔池,造成高溫鋼的次數(shù)較多。為了增加超音速氧槍吹煉條件下的鐵水的熱兌比例,主要手段有:配加低碳的直接還原鐵,氧化鐵皮,作為成渣的輔助熔劑,提高成渣速度,為脫磷反應(yīng)創(chuàng)造條件,同時(shí)為鋼渣界面脫碳反應(yīng)的進(jìn)行提供了可靠的保證。加入量的多少根據(jù)加入鐵水的具體量來確定,鐵水量較大時(shí),可以提高加入量,反之亦然。最經(jīng)濟(jì)的加入量是鐵水量的10%~40%。采用自耗式氧槍和超音速氧槍復(fù)合吹煉方式。使用自耗式氧槍作為輔助供氧手段。利用自耗式氧槍的優(yōu)點(diǎn)彌補(bǔ)超音速氧槍的缺點(diǎn),超音速氧槍主要進(jìn)行脫碳反應(yīng)的控制,爐門氧槍進(jìn)行化渣操作,沿著鋼渣界面吹氧,取得的效果要比超音速氧槍單獨(dú)吹煉的效果好。采用爐門超音速氧槍和爐壁超音速集束氧槍復(fù)合吹煉。由于超音速氧槍受熔池深度的影響,在爐底較深的情況下,射流長度達(dá)不到鋼渣界面或者鋼液內(nèi)部,利用超音速集束氧槍射流較長的優(yōu)點(diǎn),達(dá)到二者互補(bǔ)的目的,增加鐵水的熱兌比例。在一批料的時(shí)候,加強(qiáng)熔化期的吹氧脫碳的操作。減輕氧化期的脫碳任務(wù)。及時(shí)的修補(bǔ)或者挖補(bǔ)爐底,保持爐底合理的尺寸,使得超音速氧槍吹煉條件下的射流能夠較較容易的穿透鋼渣界面,降低操作難度。超音速氧槍吹煉條件下,對(duì)于爐渣的堿度要求較高,堿度既不能過大,也不能過小,理想的范圍是:二元堿度維持在2.0~3.5之間。電爐對(duì)于廢鋼在廢鋼料場向料籃配加主要的要求有哪些?進(jìn)行配料操作前從主控室計(jì)算機(jī)畫面上調(diào)出由調(diào)度站傳來的當(dāng)班生產(chǎn)調(diào)度信息或直接與值班調(diào)度聯(lián)系,確定本班的配料要求(即每爐鐵水、生鐵塊及廢鋼的加入比例)。料籃中渣料的配加操作和廢鋼的配加需要注意:料籃中物料的加入順序是:石灰→白云石→焦碳→廢鋼(含生鐵塊)。石灰加入量的確定:對(duì)于普通建筑鋼,全廢鋼兩料籃料操作時(shí),按大約2.5%~3.5%的金屬加入量來配加石灰;對(duì)于質(zhì)量要求比較高的鋼種,電爐冶煉石灰加入量按普通鋼種的1.1~1.2倍計(jì)算。采用加生鐵塊、兌鐵水需要一料籃料操作時(shí),基本石灰加入量仍然按上述比例計(jì)算,但是每增加1t鐵水或生鐵塊需額外增加20~25Kg的石灰加入量。白云石的加入量按石灰加入量的20%~25%計(jì)算??紤]到直流電弧爐對(duì)爐料導(dǎo)電性的特殊要求,如果冶煉采用全廢鋼兩次或三次加料操作時(shí),渣料(石灰、焦碳及白云石)均不應(yīng)在第一料籃加入,應(yīng)視具體情況第二料籃或第三料籃內(nèi)一次加入爐內(nèi)。交流電爐可以將渣料分為兩批加入,第二批的渣料應(yīng)該比第一批要多200~500kg。 電爐焦碳的配加量應(yīng)根據(jù)鋼種而定,一般情況下,爐料中配碳量高于鋼種上限C含量0.3%~1.2%。對(duì)于不同鋼種所需的熔清后的脫碳量,原則上非合金鋼為大于0.1%,合金鋼為大于0.3%。采用全廢鋼兩次加料操作時(shí),所有焦碳在第二料籃全部加入爐內(nèi)。電爐有一定的脫P(yáng)能力,但P過高會(huì)造成電耗增加和冶煉時(shí)間延長,因此配料時(shí)應(yīng)注意使?fàn)t料中P小于0.10%。如果冶煉鋼種對(duì)P含量有特殊要求,則要按要求進(jìn)行配料,配加低磷或者高磷廢鋼。裝入量要求:裝入量的控制應(yīng)以出鋼量及留鋼量穩(wěn)定、適當(dāng)為前提。原則上應(yīng)確保出鋼量穩(wěn)定在電爐的公稱容量±2t左右,同時(shí)應(yīng)確保爐內(nèi)留鋼量在10t左右。應(yīng)根據(jù)前一爐留鋼量確定適當(dāng)?shù)难b入量。新爐襯前2爐使用全廢鋼配料操作。在使用全廢鋼兩次加料操作時(shí),原則上第一料籃應(yīng)加入總加入量的65~75%,其余的在第二料籃加入。正常冶煉按電爐公稱容量的出鋼量進(jìn)行配料操作,鋼鐵料收得率按90~95%計(jì)算。如果需要補(bǔ)爐底或其它情況需將鋼水出盡時(shí),應(yīng)從出倒空爐子前兩爐開始逐步減少廢鋼加入量,倒空爐的配料按公稱出鋼量進(jìn)行配加,以滿足正常出鋼的要求,同時(shí)不配加白云石,以降低爐渣的粘度便于將爐渣倒干凈。具體的廢鋼配加量視爐內(nèi)的實(shí)際留鋼量定。廢鋼配料順序:料籃中各類廢鋼的加入順序是輕薄廢鋼(鋼板、輕統(tǒng)型廢鋼)→中型廢鋼(打包料、統(tǒng)料型廢鋼或生鐵塊)→重型廢鋼→輕薄料(或輕統(tǒng)型廢鋼)。但應(yīng)注意不要將大(重)型廢鋼裝在料籃中部靠近爐門的一側(cè),以免影響爐門碳氧槍的使用。對(duì)于采用爐壁碳氧槍以及超音速集束氧槍吹煉的電爐配料,大塊和難熔廢鋼,應(yīng)該避免加在氧槍的吹煉正前方。各種類型廢鋼加入量的控制:輕薄廢鋼按料籃總加入量的30~50%進(jìn)行配加,料籃底部和料籃頂部各加一半;中型廢鋼按料籃總加入量 的30~40%進(jìn)行配加,但打包料的加入量不得超過10%;重型廢鋼應(yīng)控制在加入量的20%以內(nèi)。由于重型廢鋼對(duì)爐底沖擊大,不利于提高底電極壽命,因而單重大于500Kg、小于1000Kg的重型廢鋼每爐配加不得超過1塊且只能在第一料籃內(nèi)加入此類廢鋼。此外,如果爐子是冷爐子或新爐子時(shí),嚴(yán)禁使用任何類型的重型廢鋼。考慮到電爐供氧方式,供氧能力和電爐的脫碳能力,因而電爐生鐵的配加量應(yīng)控制在一定的范圍以內(nèi),不同鋼種對(duì)生鐵配加量的要求,按照分鋼種工藝指導(dǎo)卡進(jìn)行配加??紤]到不同鋼種對(duì)殘余元素的不同要求,配料必須滿足冶煉鋼種對(duì)各種元素(尤其是殘余元素)的要求。如果冶煉鋼種對(duì)某種不易氧化元素有特殊的要求,可在配料時(shí)加入含有該元素的合金廢鋼。料藍(lán)中料位不得過高,以保證加料及冶煉過程的順利進(jìn)行。入爐廢鋼、生鐵必須符合技術(shù)要求,配料過程應(yīng)認(rèn)真負(fù)責(zé),杜絕不合格爐料入爐。配料時(shí)應(yīng)注意,不得將非導(dǎo)電的物料加在料籃中上部,以免影響爐子送電起弧。 廢鋼配料必須根據(jù)由主控室傳來的配料單進(jìn)行,每一料籃的配料單必須經(jīng)當(dāng)班煉鋼工或煉鋼助手確認(rèn)后方可通過合金計(jì)算機(jī)下傳至廢鋼配料操作室,或者電話通知廢鋼配料間。 料藍(lán)裝料結(jié)束后,應(yīng)將對(duì)應(yīng)料籃的全部信息通過配料計(jì)算機(jī)或者電話傳送至爐前主控室。電爐對(duì)于石灰有何要求?電爐煉鋼對(duì)所用石灰的主要要求有:石灰中氧化鈣越高超工好,其他雜質(zhì)(如:SiO2、P、S)應(yīng)盡量少。氧化鈣是堿性電爐爐渣中最重要的成分,爐渣中氧化鈣含量越高,則爐渣堿度就高,爐渣去除鋼中有害雜質(zhì)磷、硫的能力就強(qiáng)。石灰中的雜質(zhì)二氧化硅高時(shí),就需多加石灰,增大了渣量,而大量爐渣的熔化和加熱就增加了電能的消耗量。石灰的硫含量也應(yīng)盡量少(不高于0.05%~0.10%);冶煉優(yōu)鋼時(shí),必須使用新焙燒的石灰。由于石灰粉末極易吸水,加入爐中分解為氫和氧,造成爐氣中氫的分壓增加,從而使氫在鋼水中的溶解度也增加,使鋼中含氣量增加,嚴(yán)重影響鋼的質(zhì)量。所以原則上不允許使用石灰粉末。石灰在運(yùn)輸時(shí)要注意避免受到雨水和冰雪的襲擊受潮粉化,使用時(shí)要烘烤.對(duì)于人工加入爐內(nèi)的石灰,粒度控制范圍一般為20~100mm,最大不超過120mm。對(duì)于采用料倉加入爐內(nèi)的石灰,粒度控制在10~50mm.石灰必須配加在料籃底部,或者在加料前使用料斗子將石灰加在爐底,不能夠把石灰大量的加在電極極心園附近.電爐的配料操作有哪些內(nèi)容?電爐煉鋼的配料是煉鋼的一項(xiàng)很重要的準(zhǔn)備工作,它直接影響到冶煉的速度和鋼的質(zhì)量以及爐體壽命、金屬收得率等。合理的配料,對(duì)爐前控制化學(xué)成比較有利。配料操作時(shí)必須注意以下幾點(diǎn):嚴(yán)格按冶煉鋼種的要求或配料單配料,爐料中間的含碳量,必須根據(jù)鋼種的要求配加,含磷、硫量不得過高.廢鋼的磷、硫含量各不得大于0.08%,以保證熔清鋼水的化學(xué)成分與計(jì)算的偏差不大。料的大小要按比例搭配,以達(dá)到好裝、快化的目的.爐料要經(jīng)過稱量,做到重量準(zhǔn)確,以保證出鋼量準(zhǔn)確,特別是冶煉高合金鋼時(shí),合金成分較高,稱量不準(zhǔn),會(huì)造成大量補(bǔ)加合金,造成鋼水量不穩(wěn)定,對(duì)于模鑄的生產(chǎn)造成沖擊。爐料的好壞要按鋼種質(zhì)量要求和冶煉方法來搭配。如果使用不好的爐料,必須充分估計(jì)其收得率;清除爐料中的泥沙等酸性物質(zhì),以免熔煉過程中降低爐渣堿度。爐料中的爆炸物、密閉狀的管子或者容器必須揀出或進(jìn)行開孔處理以后,方可加入爐內(nèi)。普通電爐的攪拌能力較弱,加上升溫速度較慢,吹氧的壓力小,機(jī)械化程度低,所以為了減少操作的壓力和爐前工的勞動(dòng)強(qiáng)度,應(yīng)該避免單重大于500kg的大塊廢鋼入爐.由于在較低冶煉溫度下,硅、錳、鈦、鉻等元素與氧的親和力均比碳與氧的親和力大,熔化期這些元素比碳早氧化,這就是推遲和減緩了碳的氧化作用。因此,當(dāng)爐料中這些元素含量高時(shí),相應(yīng)地碳的氧化損失就小,就要適當(dāng)減少配碳量。對(duì)采用不氧化法冶煉的爐料要求純潔干燥。冶煉高合金鋼時(shí),應(yīng)該避免使用銹蝕嚴(yán)重的廢鋼;對(duì)于入爐的廢鋼中間不允許有成套的機(jī)器、設(shè)備及結(jié)構(gòu)件.實(shí)踐證明,好的煉鋼工配好料,爐前工的勞動(dòng)量減少一半,而且鋼的質(zhì)量也會(huì)明顯提高.電爐使用的螢石有何要求?螢石的主要成分是氟化鈣(CaF2)和CaO。主要是用來化渣和調(diào)整爐渣的粘度.所以要求螢石CaF2要高,而SiO2和S要低。一般情況下,螢石中SiO2的含量要求低于20%,特殊鋼冶煉用的螢石,比如冶煉鋁鎮(zhèn)靜鋼使用的螢石,要求SiO2的含量要低于5%.電爐廢棄的鎂碳磚破碎以后如何利用?電爐爐襯和鋼包磚大部分使用鎂碳磚制成的。將MgO-C磚及鋼包磚破碎后,作為白云石的替代品,每爐配150~200Kg的輕燒白云石和100~150Kg的破碎鎂磚進(jìn)行生產(chǎn),爐渣堿度維持1.8~2.2之間爐渣發(fā)泡能力略有過剩。泡沫渣能滿足全程的冶煉需要,爐襯的侵蝕速度也得到了有效緩解。破碎鎂碳磚的主要成分如下表MgOSiCCaOT.CH2OPS≥578.0±24.0±222.0±2≤0.5≤0.08≤0.08電爐煉鋼廠產(chǎn)生的除塵灰的成分是什么?如何利用?電爐除塵灰主要成分成分TFeSiO2CaOMgOPbZn含量%47.734.446.83.861~4.64.5~7.2由于電爐除塵灰含有Zn,用于高爐煉鐵會(huì)影響料柱的透氣性,從而影響高爐爐缸內(nèi)部的溫度分布,負(fù)面影響較多,所以電爐除塵灰添加焦油做為粘結(jié)劑,成為電爐的泡沫渣的改質(zhì)劑,寶鋼150t電爐使用介紹的效果明顯?;蛘唠姞t除塵灰可以經(jīng)過提取鋅和鉛以后,回收的鋅和鉛就可以回報(bào)處理費(fèi)用,剩余的含鐵的剩余物就可以用于燒結(jié)或者煉鐵了,但是電爐的除塵灰由于含有鉛和鋅,屬于有毒廢棄物,切不可隨意排放。電爐煉鋼廠連鑄和軋鋼工序產(chǎn)生的氧化鐵皮的成分是什么?如何利用?連鑄產(chǎn)生氧化鐵皮成分見下表成分Fe+FeOSiO2水分含量%>680.050.5~3.5氧化鐵是渣料的輔助溶劑,將氧化鐵皮應(yīng)用于熱裝鐵水生產(chǎn)低P優(yōu)質(zhì)鋼的熔劑,在[C]、[P]高時(shí),隨著螢石、石灰一起加入,作為留碳脫[P]的脫[P]劑,使用效果非常好,其中氧耗和石灰的使用量明顯降低,并且爐渣返干的比例大幅度降低,留碳脫磷命中率提高25%以上。在高比例熱裝鐵水時(shí)將氧化鐵皮和石灰一起加入作為熔化的脫磷劑,和廢鋼一起裝料加入,使用后應(yīng)用效果良好電爐配料避免硫高磷高的措施有哪些?避免磷硫過高廢鋼配加的操作要點(diǎn):生鐵磷硫含量不穩(wěn)定,使用生鐵必須抽檢化驗(yàn)以后,成分合格方可使用。廢鋼中間含有高硫物質(zhì)的原料嚴(yán)禁入爐,此類物質(zhì)包括汽車,自行車輪胎等橡膠產(chǎn)品,各類車輛的切割成形部件(易切削鋼),炮彈鋼,醫(yī)藥行業(yè)的廢棄蒸餾罐,外購不合格生鐵,以及廢舊暖氣包。此外考慮到脫硫渣在佳域渣場處理,為了防止脫硫渣球磨以后流入第二煉鋼廠,電爐冶煉低磷低硫鋼種時(shí)嚴(yán)禁消化粒鋼。嚴(yán)格禁止配加高磷廢鋼入爐。此類廢鋼包括鑄件(鑄鋼時(shí)為了改善鋼水的流動(dòng)性往往添加磷,提高鑄件的成形性能),各類汽車火車廂板(高磷耐候鋼板),廢品生鐵,以及廢舊暖氣包等。鋼中氣體通常是指哪些氣體?來源何處?各有什么危害?答:通常指氫和氮。氫來源于爐氣、原材料、冶煉和澆注系統(tǒng)的耐火材料;氮來源于氧氣、爐氣和大氣、金屬爐料。氫在鋼液中的溶解度大于它在固態(tài)鋼中的溶解度,所以在鋼液凝固過程中,氫會(huì)和CO、氮等一起析出,造成皮下氣泡,促進(jìn)中心縮孔和顯微孔隙的形成。氮在鋼液的溶解度遠(yuǎn)高于其在室溫下的溶解度,因此,鋼中的氮含量高時(shí),在低溫下呈過飽和狀態(tài)。由于氮化物在低溫時(shí)很穩(wěn)定,鋼中氮不會(huì)以氣態(tài)逸出,而是呈彌散的固態(tài)氮化物析出,結(jié)果引起金屬晶格的扭曲并產(chǎn)生巨大的內(nèi)應(yīng)力,引起鋼的硬度、脆性增加,塑性、韌性降低。原料中間鐵水,生鐵含氮量最高,焦炭,炭粉的含氮量也較高;所有含有水分的原料,生銹的原料,含有油脂類的原料,氫含量較高。電爐EBT填料的種類有哪些?成分范圍如何?EBT填料通常有鎂硅質(zhì),鎂鋁質(zhì),鉻鎂質(zhì),鈣鎂橄欖石質(zhì)等幾種,下表是兩種常見的填料的化學(xué)成分和物理參數(shù)。類別成分%物理參數(shù)項(xiàng)目MgOA1203CaOFe2O3SiO2堆積密度g/cm2粒度mm填料一填料二88.470.982.46.00.9141.850.460.67.739.11.742~51.72~5生白云石造渣的目的是什么?答:采用白云石造渣主要目的是延長爐襯壽命,其基本原理是根據(jù)氧化鎂在渣中有一定溶解度的特點(diǎn),向爐內(nèi)加入一定數(shù)量的白云石,使渣中的氧化鎂接近飽和,從而減弱熔渣對(duì)鎂質(zhì)爐襯中氧化鎂的溶解;渣中氧化鎂過飽和狀態(tài)而有少量的固態(tài)氧化鎂顆粒析出。使?fàn)t渣黏度生高,掛在爐襯表面,形成保護(hù)層。粘土磚的成分和作用是什么?答:廢粘土磚的主要成分為SiO258%-70%,Al2O327%-35%,F(xiàn)e2O31.3-2.2%。它也有稀釋爐渣的作用,但是降低爐渣的堿度,因此,只有在爐渣堿度足夠的條件下方可使用。電爐入爐主原料中,為什么要配碳?答:爐料中的碳含量應(yīng)保證氧化期有足夠的碳進(jìn)行碳氧反應(yīng),以達(dá)到去氣、去夾雜的目的。爐料中的配碳量可根據(jù)熔化期的燒損、氧化期的脫碳量和還原期的增碳量三方面來確定。電爐使用的廢鋼有哪些要求?主要檢測何種放射性物質(zhì)?具有放射性的廢鋼產(chǎn)生的輻射,不僅會(huì)污染環(huán)境,還會(huì)造成接觸放射性廢鋼的職工健康的傷害,身體產(chǎn)生病變。由于放射性物質(zhì)及其不穩(wěn)定會(huì)發(fā)生衰變,產(chǎn)生的射線有α,β和γ射線。其中α和β射線的電離能力強(qiáng)而穿透物質(zhì)的能力弱,容易被物質(zhì)屏蔽,γ射線電離能力弱而穿透物質(zhì)的能力強(qiáng),能夠殺死它能夠穿過人體部位的細(xì)胞和組織,故放射性物質(zhì)的檢測只能夠檢測γ射線檢測放射性物質(zhì)的操作有哪些基本要求?檢測要求如下:
① 必須指定專人進(jìn)行放射性污染物的檢測,檢測前穿戴好防護(hù)用品。檢測應(yīng)以一節(jié)火車車皮或單輛汽車所載運(yùn)的廢鋼鐵為檢測對(duì)象。廢鋼鐵必須全部卸下,平鋪于平坦的地面上,堆料高度不得高于1m。卸完料后20分鐘內(nèi)即可開始檢測。測量時(shí)應(yīng)進(jìn)行巡測,即對(duì)廢鋼鐵進(jìn)行普查測量。對(duì)于廢鋼的放射性檢測有哪些程序?放射性物質(zhì)的檢測流程如下具有放射性的廢鋼主要有哪些?國產(chǎn)的廢鋼,重點(diǎn)對(duì)不銹鋼、銅、鋁、醫(yī)療器械等進(jìn)行外照射及α.β表面污染水平檢測。進(jìn)口廢鋼主要針對(duì)管子、鏈軌板、各類軍用品等。國外的不法廠商會(huì)將一些冷戰(zhàn)時(shí)期核爆的效應(yīng)物,報(bào)廢的核電裝置輸華。新疆的口岸曾經(jīng)發(fā)生過華約國家的放射性廢鋼。電爐使用的廢鋼中間為什么不能夠有大量土存在?電爐使用大量的廢鋼,在廢鋼的裝料轉(zhuǎn)運(yùn)過程中,會(huì)將地上的泥土摻入廢鋼,也有商販為盈利故意將泥土摻入廢鋼,泥土中間的土含量主要成分為二氧化硅,加入電爐會(huì)降低電爐的爐渣的堿度,引起脫碳和脫磷困難,以及石灰的加入量增加,增加了各種消耗,故必須嚴(yán)格控制電爐入爐廢鋼的土含量。筆者取樣化驗(yàn)廢鋼加料以后,廢鋼池子內(nèi)渣土的成分見下表:組元SiO2SP質(zhì)量百分?jǐn)?shù)%16~350.23~0.440.18~0.30簡述石墨電極的一些企業(yè)標(biāo)準(zhǔn)?典型的一家碳素公司UHP石墨電極企業(yè)標(biāo)準(zhǔn)技術(shù)指標(biāo)如下表項(xiàng)目1998年2001年2004年ACACACDC350~500300~400450~500550~600650~700300~400450~500500~600650~700電阻率/電極≤6.54.2~5.84.0~5.84.0~5.84.0~5.84.2~6.04.2~6.04.2~6.04.2~5.5接頭≤5.52.8~3.82.8~3.82.8~3.82.8~3.8抗折強(qiáng)度/MPa電極≥1010.5~1510.5~1510~1510~1510.5~1510~1510~1510~15接頭≥1516~2518~2518~2518~25彈性模量/GPa電極≤129~149~149~149~147~147~147~147~14接頭≤1410~1810~1810~1810~18體積密度/電極≥1.651.65~1.751.64~1.751.64~1.751.64~1.751.65~1.761.64~1.751.64~1.751.64~1.75接頭≥1.701.75~1.841.75~1.841.76~1.861.78~1.89灰分/%電極≤0.30.1~0.30.1~0.30.1~0.30.1~0.3<0.2<0.2<0.2<0.2接頭≤0.30.1~0.20.1~0.20.1~0.20.1~0.2熱膨脹系數(shù)(20~600)/10-6/℃電極≤1.41.2~1.51.2~1.51.2~1.41.2~1.41.0~1.51.0~1.51.0~1.51.0~1.4接頭≤1.60.9~1.20.9~1.30.9~1.20.9~1.2真密度/電極2.20~2.232.20~2.232.20~2.232.20~2.23接頭氣孔率/%電極20~2620~2720~2720~27接頭電弧爐工況特點(diǎn)及對(duì)石墨電極的要求有哪些?答:(1)電弧爐是利用電極在廢鋼或渣層中起弧,將電能轉(zhuǎn)化成熱能,產(chǎn)生高溫,從而熔解廢鋼加熱鋼水,一般電弧弧心溫度可達(dá)(1~2)萬℃,鋼水溫度高于1600℃(2)電極柱上接電源的二次母線,下端起弧直通鋼水,其最高電流由電源決定,截面電流密度除受集膚效應(yīng)和鄰近效應(yīng)的影響外,縱向還受截面不均和機(jī)械連接中電阻多變的影響。電極必須能承受強(qiáng)大的溫度梯度造成的徑向、軸向和切向熱應(yīng)力的破壞。(3)電阻率越低,使用時(shí)電極消耗及電耗越少;為此要求續(xù)接壓降低于5V,保證該處不起弧。(4)高溫下,電極必須有一定的強(qiáng)度,在外力作用下盡量少折斷。(5)高溫下,電極不影響被加工鋼水的質(zhì)量為什么說石墨電極是煉鋼過程中最好的電極材料?(1)優(yōu)點(diǎn):高的熔點(diǎn);良好的導(dǎo)電性;高的強(qiáng)度;氧化生成CO,CO2氣體,不會(huì)污染鋼種;可調(diào)的密度,可將抗熱震性調(diào)到最佳;價(jià)格低,易加工,是理想的工業(yè)用材料。(2)缺陷和不足:石墨的升華溫度3800℃比使用中電弧的中心溫度低得多,在當(dāng)前UHP電弧爐作業(yè)的情況下,電極的升華不僅不可避免,而且最高已達(dá)68%,接近使用極限;表面溫度達(dá)600石墨的主要性能有哪些?石墨的主要性能(1)石墨加熱后直接由固態(tài)升華為氣態(tài),升華溫度高達(dá)3800℃(2)石墨與大部分材料不同,在溫度上升時(shí),其機(jī)械強(qiáng)度上升,2000℃時(shí),石墨抗拉強(qiáng)度是室溫下的1.6倍。一般約為δ抗拉1/2δ抗折=1/4δ抗壓(3)石墨的電阻率l400℃(4)石墨的導(dǎo)熱性能好,熱膨脹系數(shù)較低,抗熱震性好。(5)石墨表面溫度大于400℃會(huì)和氧氣結(jié)合,氧化量與氣體中的氧含量、氣體流量、氧化面積和時(shí)間有關(guān)。溫度達(dá)608.89℃空氣又不太充足時(shí),就會(huì)形成CO,在空氣充足時(shí)進(jìn)一步形成CO2,溫度越高表面氧化越激烈。同時(shí)石墨在一定溫度下還能與H20發(fā)生反應(yīng):H20+C→H2+CO,進(jìn)一步加氧生成H(6)石墨易加工。(7)價(jià)格便宜,比W、Mo等高熔點(diǎn)金屬均易得。(8)石墨的真密度可達(dá)2.26g/cm3,但過高的體積密度,雖可獲得優(yōu)良的電、熱和機(jī)械性能,但同時(shí)其彈性模量增加及孔度減少,所以為得到較高的抗熱震性能,體積密度一般控制在1.65~1.85g電極消耗的機(jī)理是什么?電極是短網(wǎng)的最后一部分,它通過二根以上連接起的石墨化電極的末端產(chǎn)生強(qiáng)烈的電弧熔化爐料和加熱鋼液,即電極是把電能轉(zhuǎn)化為熱能的中心樞紐,電極工作時(shí)要受到高溫,爐氣氧化以及塌料撞擊等作用,尤其是兩根電極連接處,要比其它地方電阻大、導(dǎo)電系數(shù)低,易脫扣、氧化、脫落、折斷,因而造成電極的消耗增加。電極在煉鋼過程中,由于處在高溫環(huán)境下,其電極表面與氧產(chǎn)生碳氧反應(yīng)消耗,石墨電極在低溫下穩(wěn)定,高溫下易氧化,在空氣中一般碳制品在450℃左右開始氧化,一石墨化程度較高的石墨制品在600℃左右開始氧化,超過750℃后氧化急劇增加,且隨著溫度的升高而加劇,而在水蒸氣中加熱到900℃時(shí)被氧化。即影響石墨電極側(cè)面氧化的主要因素是高溫和氧化氣氛,這就是電極氧化消耗,特別在隨著爐門氧槍、油氧助熔、EBT集束氧槍和爐壁氧槍等新技術(shù)的相繼應(yīng)用,爐內(nèi)供氧強(qiáng)度加大,氧化氣氛增強(qiáng),使得電極消耗進(jìn)一步增加。由于電極端部與電弧直接接觸,使端部電極升華形成消耗;電極部分與熔池接觸,其碳元素被熔池吸收為侵蝕消耗;電極在運(yùn)行過程中受到電磁力、機(jī)械力及固體原料沖擊力的作用而產(chǎn)生斷裂、崩落的斷裂消耗。電弧爐電極消耗可分為化學(xué)消耗和物理損耗什么叫做電極的物理損耗?電極的物理損耗主要指電極前端消耗及側(cè)面消耗,主要是由機(jī)械外力和電磁力所引起。如電極接頭處的松動(dòng)、折斷,電極裂紋和接頭螺紋部分脫落等。造成的原因是電極本身質(zhì)量差,如強(qiáng)度低;設(shè)備方面,如電極直徑選擇不當(dāng),電極夾持器、升降和控制裝置不良等;操作方面,如裝料不當(dāng),熔化期大塊廢鋼塌落撞擊電極,兩根電極連接的不緊等。什么叫做電極的化學(xué)損耗?化學(xué)損耗主要指電極表面的消耗,包括電極端的消耗和周界的消耗。電極端部局部加熱使石墨升華和電極端部與鋼液接觸,使石墨被吸收。電極尖端消耗主要是石墨在高溫下升華和在鋼渣中熔化所致。在正常作業(yè)情況下,尖端消耗可達(dá)到電極總消耗的50%。側(cè)面消耗是電極被氧化是的主要原因,消耗量約占總消耗的40%,其氧化反應(yīng)速度與溫度密切相關(guān)。電極的化學(xué)損耗特點(diǎn)有哪些?答:1、當(dāng)溫度在550℃一750消耗的影響強(qiáng)于空氣的影響。2、當(dāng)溫度高于800℃3、電極與空氣接觸面積越大,參與氧化反應(yīng)的強(qiáng)度越大,消耗隨之增高。電極周界與鋼渣的接觸及爐氣接觸造成氧化損耗。降低電極消耗的措施目前有哪些?答:目前降低電極消耗的措施主要有以下幾點(diǎn)1、優(yōu)化供電系統(tǒng)參數(shù)供電參數(shù)是影響電極消耗的關(guān)鍵性因素。比如對(duì)于一座60噸電爐來講,選擇二次側(cè)電壓為410V,電流為23kA時(shí),可以最大限度地降低電極前端消耗。2、采用水冷式復(fù)合電極水冷復(fù)合電極是近幾年國外發(fā)展起來的一種新型電極,使用水冷復(fù)合電極煉鋼一般可降低電極消耗20%一40%。水冷復(fù)合電極由上部的水冷鋼管段及其下部的石墨工作段構(gòu)成,水冷段約占整個(gè)電極長度的l/3。由于水冷鋼管段沒有高溫氧化(石墨氧化),故減少了電極氧化,同時(shí)水冷鋼管段與夾持器之間保持良好的接觸。由于水冷段與石墨段的螺紋采用水冷式,其形狀穩(wěn)定、無破損。并可承受較大的扭矩,提高了電極接口的強(qiáng)度,從而使電極消耗顯著降低。3、采用水噴淋石墨電極防氧化機(jī)理針對(duì)電極在冶煉過程中的消耗情況,采取對(duì)石墨電極噴淋水防氧化的技術(shù)措施,即在電極夾持器的下方采用環(huán)形噴水裝置向電極表面噴水,使水沿電極表面下流,在爐蓋電極孔上方用環(huán)形管向電流表面吹壓縮空氣,使水流霧化。采用這種方法后,噸鋼電極消耗明顯下降。該新技術(shù)在超高功率電爐上首先應(yīng)用。直接水淋電極方法裝置簡單,操作方便、安全。能以少量水取得較大經(jīng)濟(jì)效果。4、電極表面涂層技術(shù)電極涂層技術(shù)是降低電極消耗簡便而行之有效的技術(shù),一般可使電極消耗降低20%左右。常用的電極涂層材料為鋁及各種陶瓷材料,其在高溫下有很強(qiáng)的抗氧化性,能有效地降低電極側(cè)表面的氧化消耗。5、采用浸漬電極浸漬電極,就是將電極浸入化學(xué)藥劑中,使電極表面與藥劑發(fā)生化學(xué)作用以提高電極的抗高溫氧化能力,使用浸漬式電極可比一般電極降低電極消耗lO%一15%左右。電極不導(dǎo)電現(xiàn)象是怎樣的一個(gè)原理?電弧爐冶煉開始,控制系統(tǒng)選定自動(dòng)工作方式起弧,此時(shí)電極控制系統(tǒng)根據(jù)每個(gè)電極升降油缸管道中設(shè)置的壓力傳感器的輸人變量監(jiān)控3根電極下降過程,電極與爐料接觸后起弧,電極控制系統(tǒng)執(zhí)行控制程序正常冶煉。如圖所示,如果1根電極(假設(shè)為1號(hào)電極)下降過程中接觸到不導(dǎo)電物料不起弧并繼續(xù)下降,進(jìn)一步接觸不導(dǎo)電物料,此時(shí)電極導(dǎo)電橫臂、升降套筒的重量由原電極升降油缸一點(diǎn)支撐瞬間變成了兩點(diǎn)支撐,液壓系統(tǒng)中壓力劇降,當(dāng)降至壓力傳感器調(diào)定壓力9MPa以下時(shí),其信號(hào)迅速通過A/D轉(zhuǎn)換器傳至電弧爐控制系統(tǒng),其程序中計(jì)時(shí)器開始工作。計(jì)時(shí)3s后,電極控制系統(tǒng)中斷該電極的自動(dòng)工作方式。并且提升該電極,同時(shí)電極控制系統(tǒng)向電弧爐控制系統(tǒng)發(fā)出NON-CONDUCTINGELECTRODE1(1號(hào)電極不導(dǎo)通)信號(hào)。這時(shí)主控臺(tái)相應(yīng)的電極不導(dǎo)通指示燈亮(報(bào)警),電弧爐監(jiān)控系統(tǒng)在控制畫面及程序中驗(yàn)證報(bào)警信息。該電極出現(xiàn)不導(dǎo)通信號(hào)后,經(jīng)電弧爐控制系統(tǒng)確認(rèn)后,電極仍恢復(fù)自動(dòng)工作狀態(tài),重新下降。電弧爐控制系統(tǒng)允許此過程15,內(nèi)連續(xù)發(fā)生3次,如果超出3次后,只能重新確認(rèn)工作方式,使電極下降直至電極接觸到導(dǎo)電物料起弧為止。這
溫馨提示
- 1. 本站所有資源如無特殊說明,都需要本地電腦安裝OFFICE2007和PDF閱讀器。圖紙軟件為CAD,CAXA,PROE,UG,SolidWorks等.壓縮文件請下載最新的WinRAR軟件解壓。
- 2. 本站的文檔不包含任何第三方提供的附件圖紙等,如果需要附件,請聯(lián)系上傳者。文件的所有權(quán)益歸上傳用戶所有。
- 3. 本站RAR壓縮包中若帶圖紙,網(wǎng)頁內(nèi)容里面會(huì)有圖紙預(yù)覽,若沒有圖紙預(yù)覽就沒有圖紙。
- 4. 未經(jīng)權(quán)益所有人同意不得將文件中的內(nèi)容挪作商業(yè)或盈利用途。
- 5. 人人文庫網(wǎng)僅提供信息存儲(chǔ)空間,僅對(duì)用戶上傳內(nèi)容的表現(xiàn)方式做保護(hù)處理,對(duì)用戶上傳分享的文檔內(nèi)容本身不做任何修改或編輯,并不能對(duì)任何下載內(nèi)容負(fù)責(zé)。
- 6. 下載文件中如有侵權(quán)或不適當(dāng)內(nèi)容,請與我們聯(lián)系,我們立即糾正。
- 7. 本站不保證下載資源的準(zhǔn)確性、安全性和完整性, 同時(shí)也不承擔(dān)用戶因使用這些下載資源對(duì)自己和他人造成任何形式的傷害或損失。
最新文檔
- 軟件著作權(quán)在科技創(chuàng)新中的推動(dòng)作用
- 飲食多樣性與營養(yǎng)支持的實(shí)踐
- 初中語文生活美文拉薩的云
- 質(zhì)量保障下的供應(yīng)商篩選標(biāo)準(zhǔn)及實(shí)踐
- 浙江鴨2025版高中生物考前特訓(xùn)選擇題快練考點(diǎn)10免疫系統(tǒng)與免疫功能含解析
- 小學(xué)數(shù)學(xué)數(shù)學(xué)故事他們?nèi)绾握J(rèn)出他的
- 財(cái)務(wù)透明度與指標(biāo)提升的相互關(guān)系
- 高效辦公環(huán)境的創(chuàng)建與項(xiàng)目綜合評(píng)估實(shí)例
- 金融市場的財(cái)務(wù)分析與預(yù)測技巧
- 跨國公司如何利用科技創(chuàng)新驅(qū)動(dòng)業(yè)務(wù)增長
- 學(xué)生心理健康一生一策檔案模板
- 《胸外按壓》課件
- 2024屆南通二模(又蘇北七市二模)數(shù)學(xué)試題
- 北師大版六年級(jí)下冊書法練習(xí)指導(dǎo)教案教學(xué)設(shè)計(jì)
- 江西省南昌市2024屆高三一模語文試題及答案解析
- 2023年小學(xué)音樂2022版新課程標(biāo)準(zhǔn)考試測試題及答案(共五套)
- 第一章村集體經(jīng)濟(jì)組織會(huì)計(jì)制度講解
- 湖北煙草公司招聘考試真題
- 2024年江蘇護(hù)理職業(yè)學(xué)院高職單招(英語/數(shù)學(xué)/語文)筆試歷年參考題庫含答案解析
- -藝術(shù)博覽會(huì)與藝術(shù)品拍賣
- 保健滋補(bǔ)品行業(yè)報(bào)告
評(píng)論
0/150
提交評(píng)論